BladeStop safety bandsaws reduce the risk of serious injury
Certified by DGUV Germany
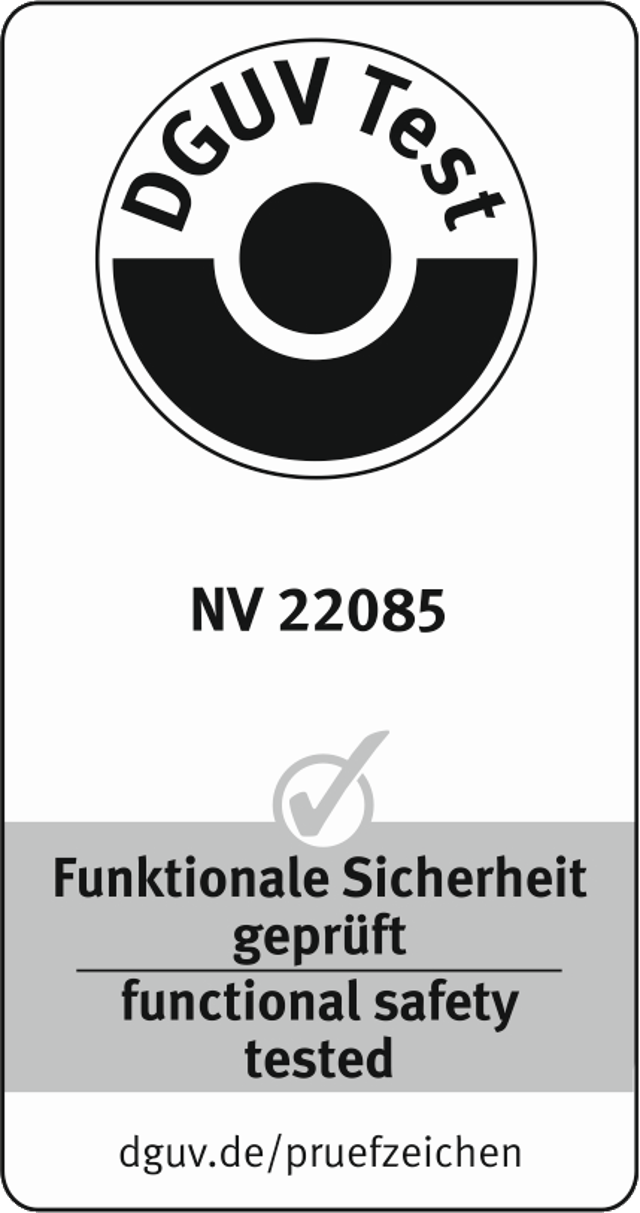
Bandsaws are typically one of the most dangerous pieces of cutting equipment used in protein and industrial processing plants, but BladeStop is designed to be both safe and easy to operate. The award-winning design is uncomplicated and user-friendly with unbeatable safety features. BladeStop are the only bandsaws certified for their functional safety by internationally recognised testing organisation DGUV Germany.
Bandsaws are used in a wide variety of industries with multiple applications and processing requirements. Our biggest design challenge was to develop a solution which would be applicable not just to operators carrying out slow and controlled cuts, but also those cutting at high speeds and volumes. Additional consideration was also required for the various operator hand placements to control the product going through the blade. This factor could vary significantly depending on customer-specific applications. Thus, the two most critical variables in our development process were speed and operator monitoring.
To accommodate the high-speed cutting applications, we developed a microcontroller-based system paired with the fastest mechanically actuated blade clamping mechanism on the market, capable of stopping the blade in under 10 milliseconds.
Development challenges
Bandsaws are used in a wide variety of industries with multiple applications and processing requirements. Our biggest design challenge was to develop a solution which would be applicable not just to operators carrying out slow and controlled cuts, but also those cutting at high speeds and volumes. Additional consideration was also required for the various operator hand placements to control the product going through the blade. This factor could vary significantly depending on customer-specific applications. Thus, the two most critical variables in our development process were speed and operator monitoring.
To accommodate the high-speed cutting applications, we developed a microcontroller-based system paired with the fastest mechanically actuated blade clamping mechanism on the market, capable of stopping the blade in under 10 milliseconds.
Unique Dual-Sensing-System
To address operator monitoring accuracy, we opted for a “dual-sensing” system using a combination of two technologies:
1) GloveCheck™ Vision Sensing – This vision system was developed by Scott as a solution to significantly reduce risk of serious injury. Our high-speed vision system is continuously monitoring both the colour of the operators glove along with their movements; if their trajectory is calculated to result in contact with the blade, the patented BladeStop braking-mechanism stops the blade before an operator comes into contact with it. This results in most operators walking away from the saw without a scratch.
2) Body-Sensing Technology – A revolutionary world-first system which monitors not just the operators’ fingers, but their entire body. Our advanced control system is continuously looking out for contact between the operators’ skin and the saw blade, even when not in direct line of sight on our GloveCheck system. The innovative sensing system can distinguish the difference between human flesh and the product being processed. It is this sensing system, paired with the fastest stopping time on the market, which makes it possible for the operator to walk away from an incident with a minor cut rather than a serious amputation.
Considering the Cost
Considering the Cost
When we review the commerciality and value proposition of BladeStop, it is often easy to just compare the cost to tend the injury against the cost of the saw, however, there are many real factors to consider underneath the surface.
Direct Financial Impact
• Workers’ compensation costs.
• Legal fees
• Medical costs
• Rehabilitation costs
• Insurance premiums
• Production down-time
Indirect Impact
• Psychological trauma of the victim
• Psychological trauma of the colleagues
• Impact on reputation for the business.
• Global impact on brand
Band saw safety as added value for companies
Band saw safety as added value for companies
BladeStop has made a significant impact on safety culture around bandsaw operation in the industry. Recent statistics from Safe Work Australia has outlined a 23% reduction in serious injury claim frequency from 2010 to 2019, with BladeStop saws making a significant contribution to this figure via multiple saves recorded yearly. Since bandsaw operators are regularly faced with repetitive and labour-intensive duties, the implementation of BladeStop has led to a marked improvement in quality of life for these hard-working individuals around the world.
For businesses around the world, BladeStop has shown to make a positive impact on performance by providing peace of mind, thereby boosting productivity. BladeStop has given businesses the opportunity to show leadership by investing in their people. By investing in BladeStop™ our clients are showing the world they are committed to employee safety and wellbeing as well as bolstering safety initiatives. This results in strong brand loyalty and a subsequent increasing sales through social responsibility.
BladeStop has set the benchmark for bandsaw safety in the industry globally, with a strong foothold in Australasia, USA and Europe. Expanding into new markets and actively educating customers of the risks vs benefits has been our mission to ensure operators are protected globally.