Digital warehouse management
Highly-automated storage and retrieval
In Bolzano, Italy, a highly-automated warehouse system is operating around the clock five and a half days a week, relieving the staff's workload and balancing out a possible shortage of skilled workers. The team from Westfalia Technologies planned and implemented it for Mila – Bergmilch Südtirol. The compact, automated satellite warehouse is linked to the processing of more than 200,000 tonnes of milk per year. A central conveying line in the fresh produce warehouse transports the goods from the production department to the warehouse and the picking halls. The fresh produce warehouse is around 44 metres long, approximately 23 metres wide and, with a height of 17 metres, accommodates eight levels, each with storage channels that are up to four bays deep and around 4,140 storage spaces. Chain satellites are used for the triple rails. Each hour, they store 65 pallets in double cycles and 62 pallets in single cycles. Two lateral retrieval conveyors with a total length of 20 metres are also in operation between the refrigerated warehouse and the picking halls.
Management of storage spaces, stocks and warehouses
However, Westfalia Technologies not only updated the automated warehouse system to its current technological level in terms of systems technology, but also in terms of software: "As a long-term customer, Mila has implemented all four generations of our software since 1994, starting with a simple warehouse management system", explains Christian Goltermann, Head of Software & IT Sales. "Savanna.NET has since developed into a Warehouse Execution System that combines warehouse management and material flow control. Following the Savanna upgrades to version 2.15, we implemented functional extensions in parallel with the construction phases." These include the management of storage spaces, stock and warehouses, material flow control, coupling with the SAP ERP system and stock booking via mobile data terminals on the responsive user interface. "We have extended the functional scope by manual storage spaces in the new picking department, automatic replenishment from the high bay warehouse and storage space management for the two picking zones using mobile terminals", says Goltermann.
Storage and retrieval logic reduces re-storage processes and enables warehouse capacity to be optimally exploited. The IT team has switched scanner communication from a serial connection to a TCP/IP network connection, and has implemented the interfaces to the new automated storage and retrieval units and the extended materials handling technology by means of software. A Microsoft SQL server has been set up as the central database. "Thanks to Savanna, picking in the new picking zones is carried out using hand-held terminals and instructions are given to the system decentrally", states Thomas Bernhart, Technical Director of Mila – Bergmilch Südtirol, summing up the benefits of this modernisation.
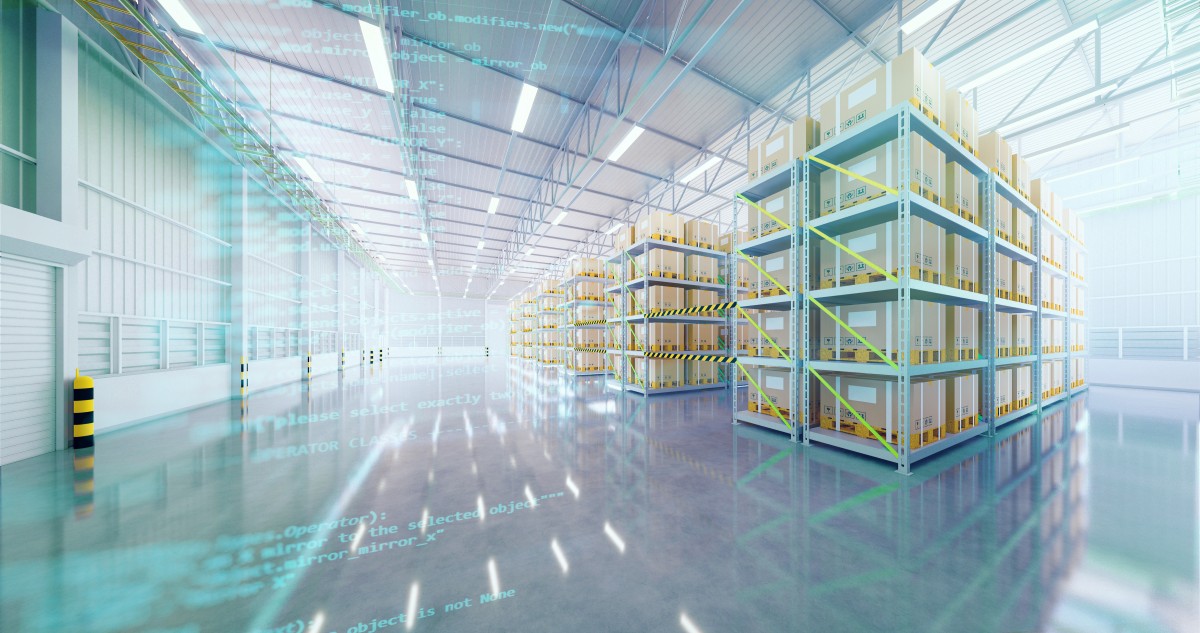
© SSI Schäfer GmbH & Co KG
More intelligence at operating level
This example shows that the intralogistics specialists are using the full potential of software-based systems to meet requirements in the food industry. A Warehouse Execution System (WES) comes into play wherever classic warehouse management using a Warehouse Management System (WMS) no longer suffices. As operational intelligence, it mediates between system control and order management and acts as a link between the WMS and the material flow control system. Central trends in this regard include real-time functions for managing stocks and for controlling the automated storage and retrieval units and materials handling elements throughout the entire warehouse; these will also be reflected at Anuga FoodTec in 2027. The solutions shown in Cologne also enable intervention into the material flow at any time, allow system and device diagnosis using machine data and ensure that any number of warehouses can be managed, controlled and synchronised centrally.
Fast digitalisation for SMEs
SSI Schäfer also wants to offer the consistent optimisation of all processes and components as an important step towards Intralogistics 4.0. With its WAMAS Entry-Level Solutions, the intralogistics specialist is targeting small and medium-sized enterprises (SMEs) as well as projects with a medium level of complexity. The software portfolio offers a standardised, quickly implementable option for digitalising and automating warehouse processes while ensuring high scalability. "Our goal is to enable quick and easy access to cutting-edge warehousing software that can grow along with our customers' future requirements. This means that companies benefit from a solution that actively accompanies their growth", says Florian Schneebauer, Vice President Product Line Software at SSI Schäfer. The portfolio includes the tried-and tested software modules WAMAS Core WMS, an entry-level solution for digital warehouse management, and WAMAS High Bay MFS, which controls automated high bay warehouses.
SSI Schäfer is additionally extending its digitalisation expertise with the foundation of SupplyBrain. The start-up develops data-backed software solutions that address the core areas of the supply chain. Companies can use a digital twin to simulate alternative solution approaches and determine which variant would be the most efficient if, for example, employees in the picking department are absent due to illness or order structures change significantly as a result of changed market conditions. Another service module is optimisation of the maintenance strategy towards predictive maintenance. The optimum maintenance window is determined through AI-supported analysis of the system components' usage data.
How AI is revolutionising the material flow
"Machine learning and neural networks will increase warehouse performance. Goods throughput will increase, manual and automated fleets can be optimised and staff can be used more efficiently. All in all, this will lead to significant cost reductions for companies", prophesies Ulrike Just, member of the management board of Linde MH. Linde MH's strategy initially involves networking manual industrial trucks. To achieve this, the intralogistics company is currently developing a system for real-time localisation that functions both inside warehouses and also outside of buildings. It enables seamless tracking of the location of each vehicle, for which it uses low-infrastructure ultra-broadband technology. An intelligent display provides the drivers with instructions for navigating through the warehouse or issues new or modified transport orders. To do this, the system combines location and vehicle data such as the steering angle. This enables the route to be adapted in real time if, for instance, traffic on the roads is too heavy and time would otherwise be lost.
Digital twin of the warehouse
In the second step, Linde MH intends to enable coordinated collaboration and route optimisation between manual and automated industrial trucks. "If 100 or more vehicles are to be coordinated, it can only be achieved with higher-level intelligence and hardware that can process such high volumes of data", explains Ron Winkler, Managing Director of Linde MH's Digital Business Unit. "This is where the NVIDIA Omniverse platform's AI comes into play. A digital twin of the warehouse is established, a virtual 1:1 image of the physical reality." In this digital twin, simulations can be computed in fractions of a second, either to optimise routes and optimally coordinate autonomous mobile robots (AMRs) and manual industrial trucks or to achieve optimisations in existing warehouse layouts.
Solution options for changing requirements or problems in the warehouse, such as current order or stock changes, traffic density in certain warehouse areas, obstacles or overhanging loads, are recorded in real time and simulated in the digital twin. New calculations are fed back to the vehicle control system – for instance, that a lorry whose arrival is delayed should be unloaded by the nearest forklift truck with the corresponding equipment. To do this, all physical data of the industrial trucks (e.g. engine output, steering angle) and the infrastructure (e.g. shelf spaces, routes, machine times) are stored in digital form in the Omniverse platform. The information that is continuously provided by sensors, intelligent vehicle and infrastructure cameras, warehouse management software and vehicle control systems is then processed in this virtual space.