Extraction Process Enables Utilisation of High-Quality Food Ingredients
1. What customer requirements led to the development of the ANDRITZ Turbex and on which separation technologies from your portfolio is the development based?
With the Turbex as an extraction application, ANDRITZ Separation is consistently expanding its portfolio alongside dewatering technologies and drying applications. Our customers often require more efficient, upstream extraction and fractionation of the raw materials used.
The Turbex utilises two key technological features:
- Generation and utilisation of cavitation for efficient digestion of natural raw materials in a hydrodynamic environment
- In contrast to conventional batch extraction processes, the Turbex also operates continuously and in a patented counter-current process This achieves an extraction effect that is comparable to a twelve-stage batch process.
2. What challenges had to be overcome before the product was ready for series production and patenting?
In fact, there were a number of challenges to overcome along the way. It was not so much the actual extraction process in the reactor that was affected, but rather the matrix feed into the reactor, for which the fluid properties were underestimated for some products. A quantity of solvent was also initially discharged and lost during solids discharge. This is recovered in the current system and fed back into the solvent.
3. What are the outstanding technical innovations and advantages of the process?
The process is based on the high-frequency interaction of vacuum and high particulate pressure, whereby botanical and organic raw materials are efficiently perforated "from the inside out" and provide a large contact surface for extraction. In a highly turbulent environment, generated by a multi-stage rotor-stator arrangement with up to 2,000 revolutions per minute, the mass transfer coefficient is increased almost one hundred-fold compared to conventional extraction. Counter-current extraction also keeps the gradient between the base material and solvent concentration at a constantly high level. This significantly increases the three decisive factors for mass transfer, i.e. "surface area A", "mass transfer coefficient k" and "concentration difference DC", and greatly accelerates the mass transition. This makes it possible to extract the supplied matrix in less than two minutes. At the same time, the extraction temperature can be kept at a low level - in most cases at 30 to 40°C.
4. Which traditional extraction concepts does counter-current cavitation extraction with the ANDRITZ Turbex compete with?
Comparative studies show significant advantages of the ANDRITZ Turbex over the classic one or two-stage batch process. There are also advantages in terms of extraction time and yield compared to ultrasound-based batch extraction.
Compared to other continuous counter-current extraction processes on the market, the measurable advantage is due to the cavitation effects, which enable a low extraction temperature and keep the active phenol groups of extracted antioxidants at maximum activity in the absence of oxygen.
Compared to other cavitation extractors on the market, the Turbex stands out due to its counter-current extraction and the high number of cavitation events of up to 150,000 per minute.
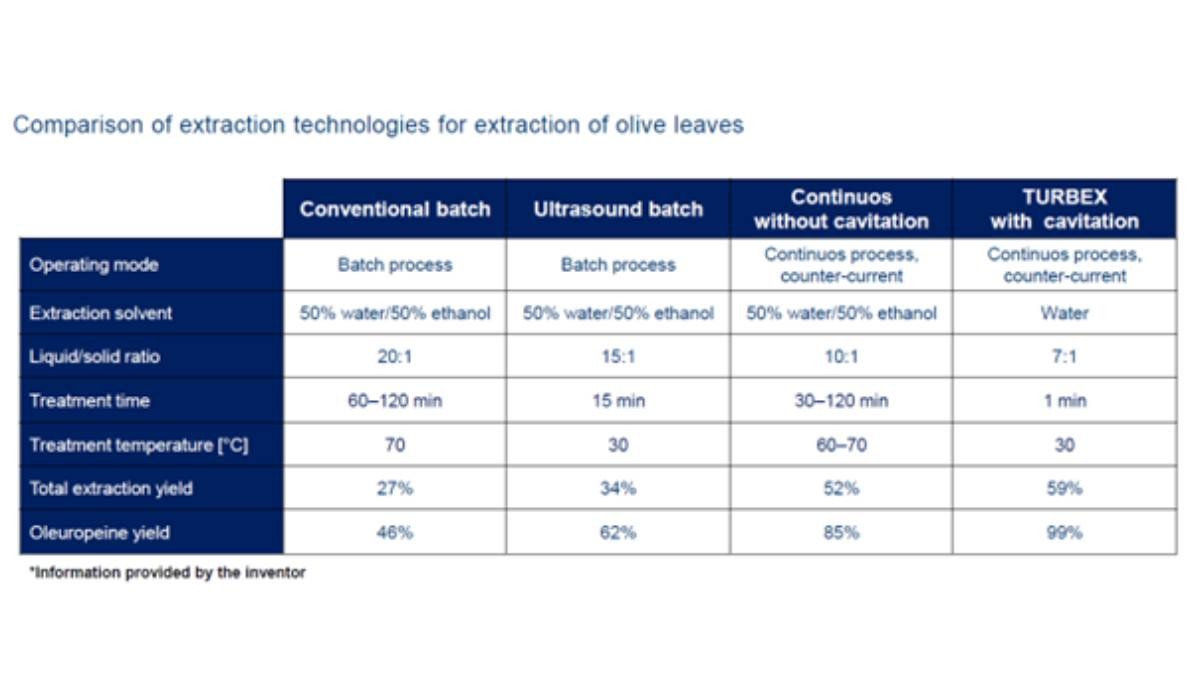
5. What potential savings does the process offer?
In most of the extraction processes tested, the yield in relation to the target molecule could be increased by at least 25 %, and in some cases by up to 80 %. The antioxidant reaction potential (ARP value) can be significantly increased, for example by a factor of five in the case of polyphenols from brewer's spent grains. In simple terms: The Turbex not only extracts significantly more product in less time, the product quality is also measurably better and the energy required for extraction is 30 % less than that of conventional extraction.
6. Which sectors of the food industry can particularly benefit from this innovation? Is the process also suitable for smaller companies?
The Turbex extraction process is aimed at extracting proteins and amino acids, polyphenols and antioxidants as well as fats and oils. The remaining solids, usually roughage and fibres, are of a dietary nature and are characterised by high porosity. In principle, the extraction of leaves, flowers, bark, roots, fruits, seeds and kernels is possible. The material fed in must be adjusted to particle sizes of less than two millimetres. As the amount of product to be processed in terms of dry matter is 200 kg per hour, the Turbex is also suitable for small and medium-sized businesses.
7. How do the respective product requirements for a gentle, value-preserving extraction process differ?
The extraction process offers various parameters that optimise the extraction by individually adjusting it to the selected target molecule. These parameters essentially include the extraction temperature, the selected solvent and the solvent concentration, the cavitation intensity and the cycle time through the reactor. In addition, the extraction medium is divided into a liquid/solid ratio for the matrix preparation and the subsequent counter-current extraction. This increases the extraction of the respective target molecules or substance groups.
8. Are ingredients oxidised or proteins denatured to a small extent or are all properties fully retained?
The short throughput time during extraction, a process temperature of 30 to 40°C, the pressurisation of the process vessels with inert gas and the resulting elimination of excess oxygen help to ensure that the active phenol groups are reduced as little as possible and their activity is maintained at the highest level. Denaturation of proteins is virtually impossible at the prevailing temperatures.
9. How do you ensure hygienic and microbiological stability when recovering and reusing the solvent in the cycle despite low process temperatures?
Various systems are integrated into the Turbex process to directly recover most of the solvents remaining in the solids and return them to the cycle. The resulting increase in the concentration of the solvent is beneficial to the overall material balance. If it makes economic sense, the entire solvent can also be recovered in a vacuum evaporation/drying process.
10. How are the extraction products obtained processed further or passed on?
This task is subject to the respective utilisation characteristics of our customers. The valuable product can be contained in the solids, in the extract obtained or in both process streams. In principle, a concentration-enriched extract can be produced as a product, but drying to powder is also possible. The latter applies to both the liquid and the solid phase.
11. Which cleaning processes are required?
The Turbex can be cleaned with all commercially available cleaning agents. Complete daily cleaning is recommended, but certainly after every product change.
12. Which models for which capacity range does the Turbex series currently comprise?
The Turbex is currently available in two ATEX versions. The first variant is aimed at customers and process requirements that need a complete extraction line. This includes the solids preparation, the reaction vessel, a feed unit on the feed side, as well as solid/liquid and liquid/solid separation at the corresponding outlets. The entire system is equipped with measurement and control technology so that all processes run fully automatically.
The second system variant is aimed at customers who already have an existing extraction line. This is where the system starts at the existing solids discharge in order to increase the extraction yield or shorten the extraction time without affecting the existing primary product process. This allows the efficiency of the offline process to be validated and qualified before the processes are combined in an inline process.
The processing quantity of up to 200 kg/h is identical for both processes - in each case in relation to the dry substance in the feed stream.
13. How can a gentle extraction of the ingredients be achieved despite more intensive extraction with energy input through shearing forces, turbulence and cavitation?
The short treatment time in the extraction reactor limits the influence of shear forces.
14. What is the economic comparison between ANDRITZ-Turbex and conventional extraction processes?
The profitability of the investment depends heavily on whether it is a new investment or a process optimisation of existing lines. At the same time, the commercial value of the manufactured product is of considerable importance. Depending on the process yield increase and product value, payback periods of 18 to 48 months are realistic. In the case of new process lines, this period is even shorter. In addition, the ANDRITZ Turbex can help our customers to achieve their ESG (Environmental, Social & Governance) goals, for example by reducing the use of solvents or using less energy in the production process.
15. What preliminary considerations should interested users make before deciding in favour of counter-current cavitation extraction?
The key question is whether a customer sees potential in an increase in process yield or whether the commercial potential lies in better product quality.
The higher the yield loss in the discharged solids, the more interesting the use of a Turbex. To evaluate this potential, ANDRITZ offers preliminary analyses and tests at a specially equipped test facility at our site near Gouda in the Netherlands. It is also possible to borrow a transportable pilot system suitable for ATEX and food applications. This allows customers to test and evaluate this new technology without risk. And our experts are on hand with their experience to provide help and advice.
Contact
ANDRITZ Separation GmbH
Thomas Wünsche, Industry Director Food & Beverage
thomas.wuensche@andritz.com
T +49-(0)1515-155615-2
www.andritz.com/separation
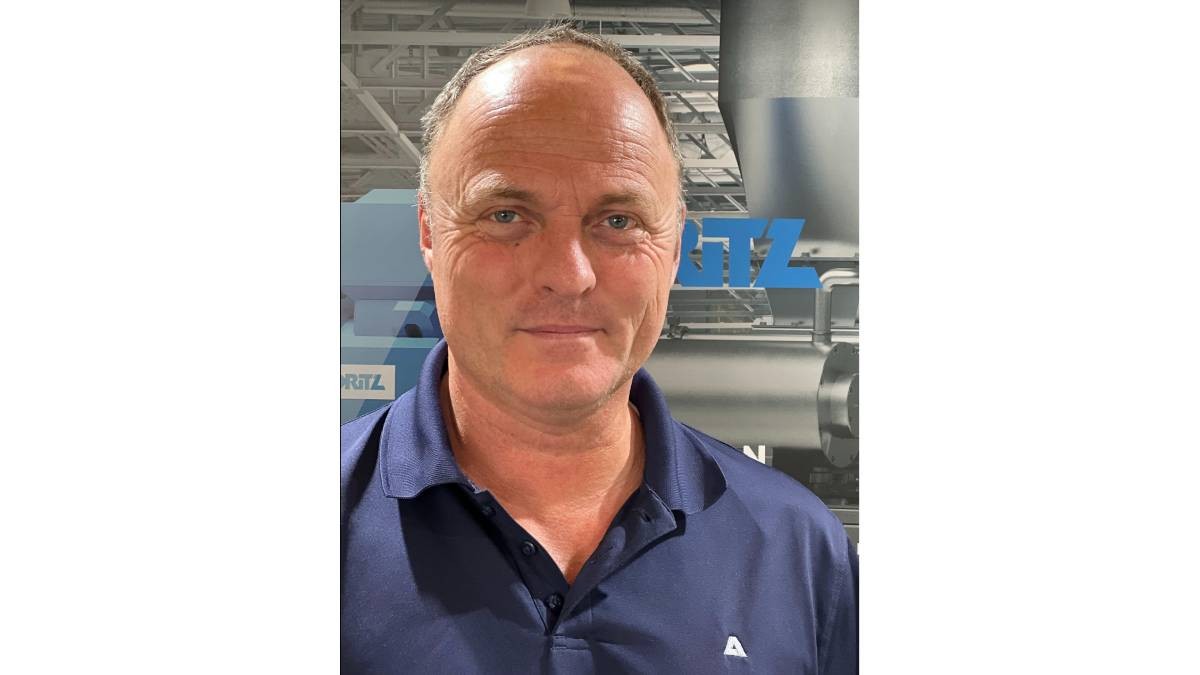