Many Core Processes Rethought
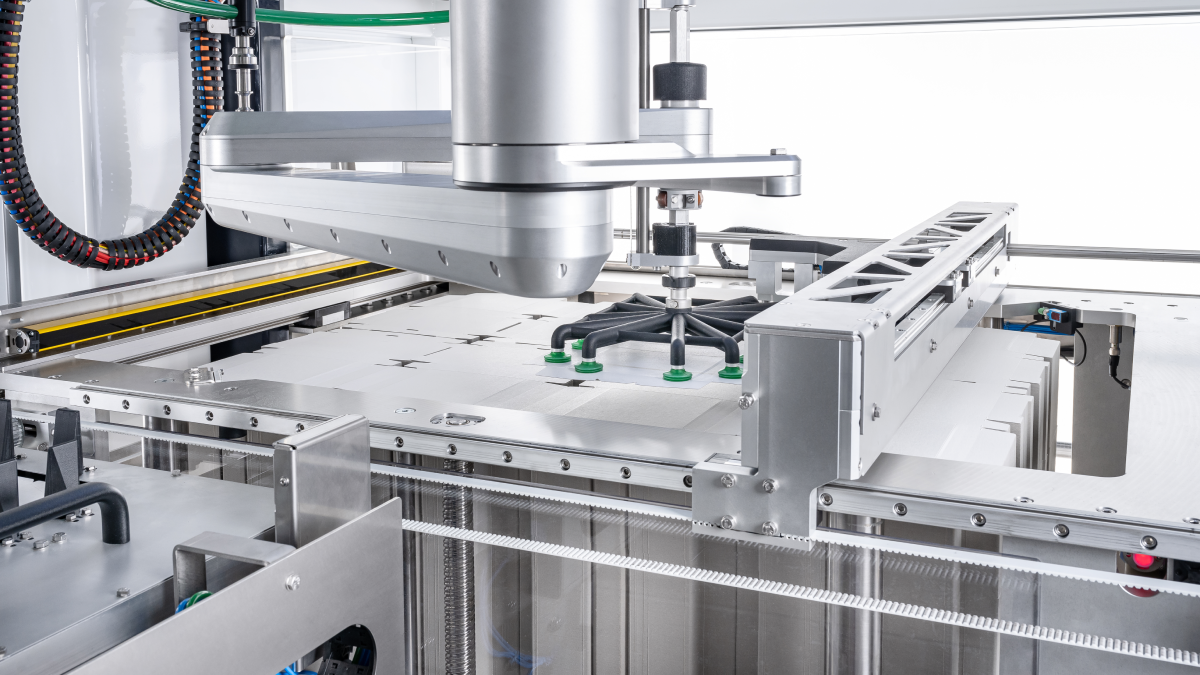
The mechanical engineering sector showcased innovative and sustainable solutions for packaging food at Anuga FoodTec 2024. At the heart of the Schubert stand: The TLM Comfort Feeder, an efficient and resource-saving solution for feeding cardboard blanks directly from the pallet. Photo: Gerhard Schubert GmbH
Scalable and flexible for many recipes
Anuga FoodTec has once again shown: Whether it's dairy products, convenience food, confectionery, delicatessen or vegan and vegetarian specialities - processing systems today must be scalable and flexible enough to achieve a high degree of energy efficiency and resource conservation, and to be able to process new ingredients in the future. This is precisely where automation and digitalisation come in, both of which are key trends at the Cologne trade fair grounds. The latest generation of moulding, filling and cutting systems for the automated production of snacks and convenience products all the way up to meat products and pet food are examples of this. Lines such as those on display at the stands of Vemag, Handtmann, K+G Wetter or Weber and many others can be converted for other applications in just a few simple steps. Multifunctional machines, like the Formax Nova-Max 400 from Provisur Technologies, are used to mould burger meat, but can also be used for products such as poultry, protein alternatives and baked goods.
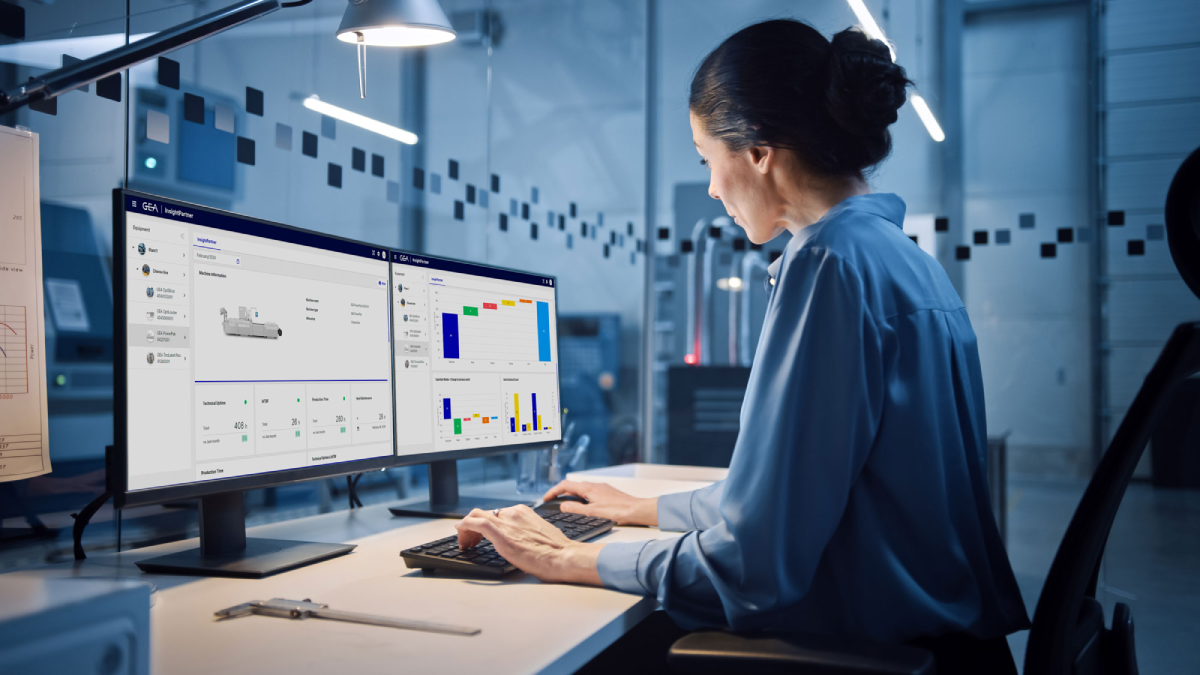
At the trade fair, GEA presented the cloud-based web application for processing and packaging lines, a new addition to the GEA Insight Partner family. Here, advanced analytics and predictive elements are integrated into continuous machine monitoring, which suggest measures for resource-saving operation. Source: GEA
Alternative proteins
Plant-based ingredients are the basis for many new recipes. In this context, innovations in process technology include a broad range of systems that realise both animal and vegan ideas. Plant-based alternatives from innovative protein sources and raw materials in particular pose technological challenges for the production process. The sensory and technofunctional properties of plant proteins change depending on how they're treated. With modern twin-screw extruders in hybrid design, one of Coperion's focal points at the trade fair, both texturised plant protein and meat analogues with a high water content can be produced with minimal changeover effort. The extrudates form the basis for a variety of reformulated burger patties, nuggets or sausages.
Whether for extruding, stirring, kneading, mixing or homogenising: The systems on display were accompanied by a variety of digital solutions that are specifically tailored to the processes and network them into an overall line. Modern recipe and batch management software makes it possible to plan and control production fully automatically.
The next step in innovation for inspection
After all, it's primarily digital technologies that provide insights into processes that were not available in the past. This trend is increasingly prevalent in the food and beverage industry. The fact that artificial intelligence plays a central role in this was also made clear at the Cologne trade fair grounds. An increasing number of optical processes with deep learning are available on the market. They make it possible to analyse food in the entire wavelength range - from ultraviolet light to the visible and near-infrared. And: The processes are contactless, which means they fulfil the demanding hygiene requirements. As optical systems determine known measured variables directly in the production process, they are developing into reliable tools for real-time quality control.
Solutions like those on exhibit in Cologne use multispectral and hyperspectral camera systems to detect foreign materials with similar or identical shapes and colours, regardless of density or material. Insort's Chemical Imaging Technology is an example of optical inspection and sorting of food products that works on the basis of near-infrared spectroscopy. It finds even the smallest product faults and defects that are invisible to the human eye and removes them from the product flow. The technology is used in the Hypernova, the latest line in the Sherlock series, which is particularly suitable for sorting small food products.
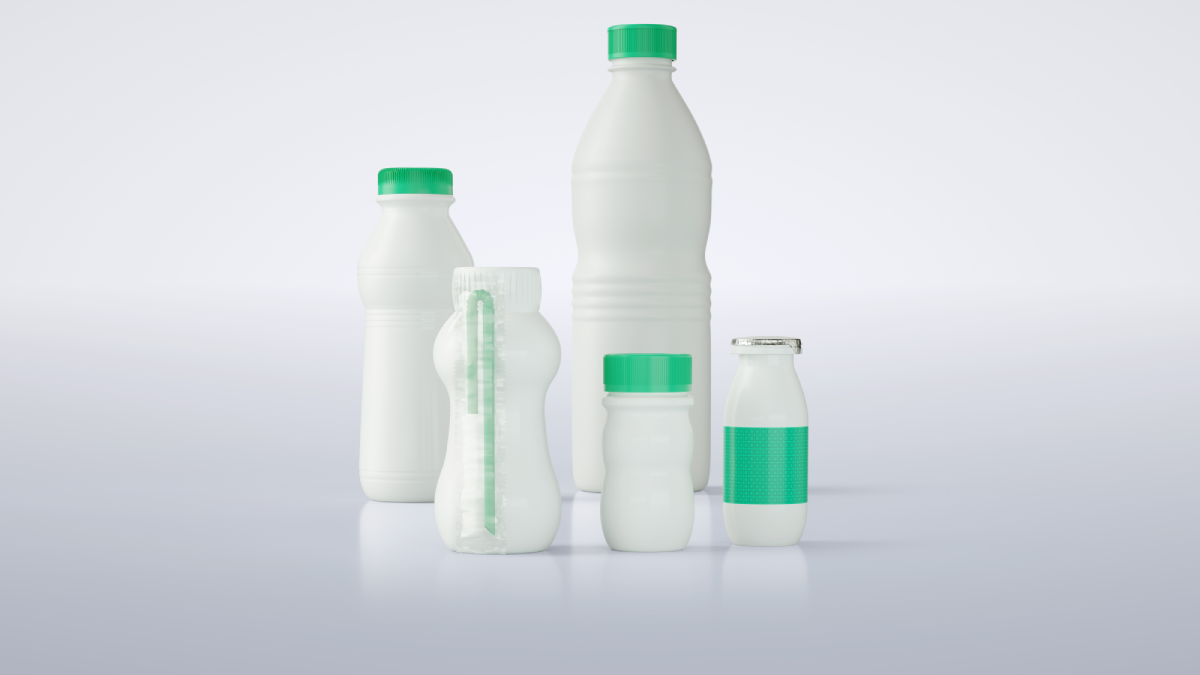
The new generation of aseptic bottling: With Syntegon's FBL, manufacturers can fill different bottle formats and materials with high efficiency and accuracy. Photo: Syntegon
More recyclable packaging
The European Union's New Green Deal is intended to ban all non-recyclable materials from packaging by 2030 at the latest. More paper instead of plastic, more recyclable monomaterials instead of multilayer films is the answer from the exhibitors at Anuga FoodTec, who are using their expertise in the field of packaging to support producers on their way to climate neutrality. When designing fully automated and robot-assisted packaging machines, the focus is increasingly on modular and easily convertible lines that can process both conventional and fully recyclable packaging. From pick-and-place robots to complete packaging lines and filling machines, the machine manufacturers in Cologne, including Sealpac, Multivac, Stäubli and Syntegon, showcased all the technologies that food and beverage manufacturers require for their high-quality packaging.
With the latest generation of high-performance packaging machines, such as those presented by Schubert with the Flowpacker, recyclable flow-wrap bags can also be produced from monofilms or paper-based films. To this end, the machine was equipped with sealing technology that allows cross-sealing using ultrasound. Another example is packaging that does not require glue. Schubert demonstrates this with Dotlock, a technology based on clinching technology for joining metals. The cardboard layers are pierced from one side with a needle, creating a collar on the other side. This is then pressed onto the carton and creates a stable positive and form fit. As a 100 percent glue-free packaging solution, Dotlock is fully recyclable via the paper cycle. The hybrid packaging consists of cardboard and thin monofilm, both of which are easy to separate and therefore fully recyclable.
Technologies that increase overall efficiency
Sustainable production is closely linked to the reduction of greenhouse gas emissions, water consumption and thermal energy as well as the switch to renewable energies. Global warming, energy dependency and rising costs are becoming increasingly pressing issues. Where can food producers start with the energy transition in order to remain competitive? The technological highlights at Anuga FoodTec 2024 clearly included technologies that enable companies to reduce their energy requirements and produce more resource-efficiently. To pave the way for climate-neutral production in the food industry, the international supply industry is focusing on fully automated process technologies that can be powered 100 percent by renewable energy.
Digital monitoring of the processes in real time in turn makes it possible to break down the energy consumption for rinsing, cleaning, washing or heating into individual processes and to adjust them if necessary. Mechanical engineering also identifies the processes in which energy can be recovered in the form of waste heat and utilised for other processes. A broad portfolio of heat pumps is available for various applications that require both heating and cooling.