One step ahead of every problem
Specialised service providers for repairs
High reject rates, inefficient machine utilisation, downtime due to unplanned maintenance activities – many processes in food production suffer from these avoidable problems. Once the red light comes on at the packaging line, it's often too late to react in time. And if it stops, the other systems in the process chain must also be shut down. This is where sustainability begins, because a requirement-oriented maintenance strategy helps to ensure that the systems remain in use for as long as possible and that no food is wasted. This is also a simple calculation from a business perspective, as machine availability is the top priority.
However, modern maintenance management presents food producers with challenges, which is ultimately reflected in the trend for an increasing number of companies to outsource this task in order to concentrate on their core business. The exhibitors at Anuga FoodTec offer service packages that include customised maintenance contracts. This outsourcing involves tasks such as maintenance, inspection or repair being outsourced to specialised service providers. Combined with retrofit solutions, training courses and training measures, this increases system availability and maintains the value of the machines over their entire life cycle.
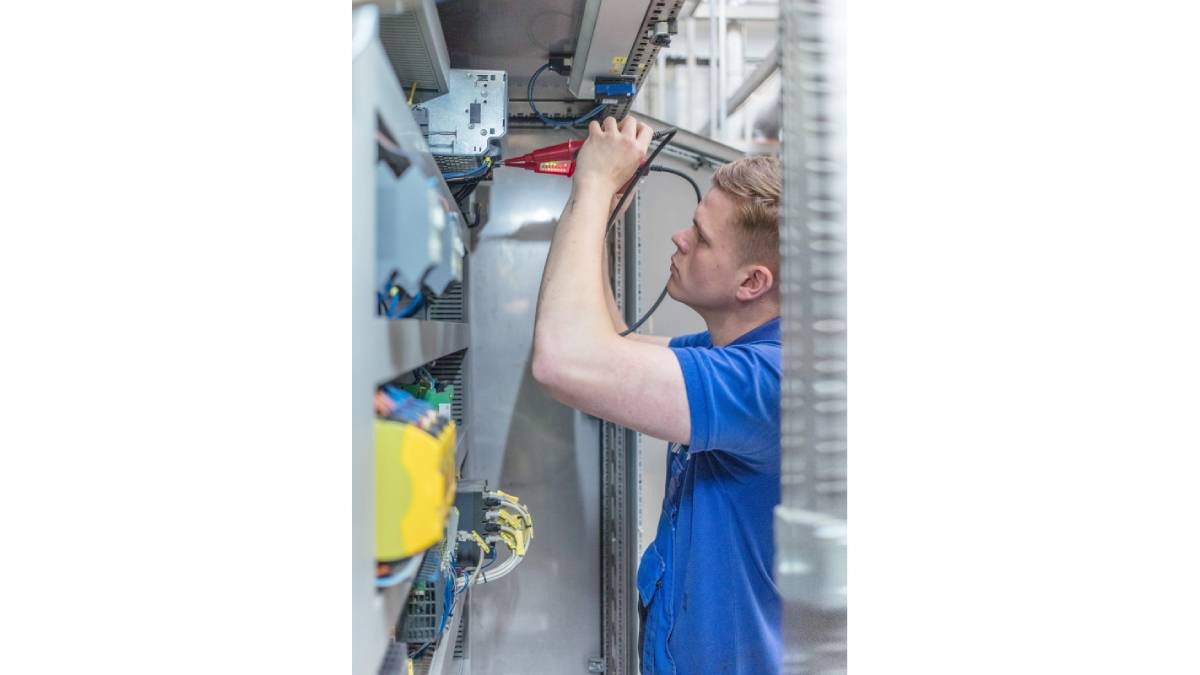
KHS service technicians check the current status of the machines on site and identify the necessary wearing and spare parts. © Frank Reinhold
Outsourcing for optimum performance
With modular service packages and individual agreements, KHS also ensures that its lines run smoothly and efficiently for beverage bottlers. This is ensured, for example, by embedded engineers, i.e. experienced technicians who are on site at the customer's premises for the entire duration of the contract. In addition to carrying out time-based and condition-based maintenance, they make suggestions for improvements to daily maintenance work and format changes, support the operating personnel in analysing and eliminating faults and identify potential for optimisation in day-to-day operations. "In comparison to conventional, reactive service, which only comes into play in the event of specific failures, productivity can be increased by up to four per cent with preventive service," explains Miriam Seilkopf, who is responsible for service contracts at KHS.
One example of such customised partnerships is the collaboration with the Paulaner brewery, which was newly built in the west of Munich in 2015. Six lines are in operation here. These are three returnable glass lines, including one for swing-top bottles, each with a capacity of up to 50,000 bottles per hour. They feature a variety of packaging options - from six-packs to cartons and crates. There is also a non-returnable glass line for export, a keg line for up to 1,000 barrels per hour and a can line originally for up to 30,000 containers per hour. The latter was replaced in 2021 by a new and significantly more efficient line with a capacity of up to 90,000 cans per hour.
The systems must be serviced regularly and, ideally, proactively. In doing so, Paulaner dispenses with year-round support from technicians on site. Nevertheless, there is a KHS coordinator who acts as an interface between the brewery group and the plant manufacturer's five German sites. He performs coordination tasks on the brewery premises and carries out administrative activities. Above all, this includes spare parts management, for which KHS maintains a consignment warehouse – less than 200 metres from the filling lines.
A look into the future of the system
There are now new services that look to the future in combination with state-of-the-art technologies such as artificial intelligence. Bundled under the term predictive maintenance, they symbolise Industry 4.0 - and that means: Precise, data-based forecasting models, combined with intelligent logistics for spare parts and 24-hour availability for support. And this is mainly achieved digitally. IoT-enabled solutions direct attention specifically to where it's needed in order to avoid failures from the outset. Even creeping changes such as deviating heat development or increasing motor currents in a system can be recognised and eliminated at an early stage so that major downtimes are reduced to an absolute minimum.
The technology providers at Anuga FoodTec offer a comprehensive range of solutions for analysing machine data: From sensors that use a standardised interface to provide additional data for efficient condition monitoring and standard systems with extensive analysis options to customised complete solutions. Thanks to improved measurement performance, the latest generation of condition monitoring sensors are able to recognise the slightest changes in condition even earlier than before. The goal: Be quicker than the problem!
In terms of maintenance, this means that sensor data is analysed in real time using smart algorithms. The measuring devices "think" for themselves, monitor themselves and help staff to rectify problems with precise instructions - and even recommend the right successor product at the end of their life cycle. All machine data, fault messages and information on operation and maintenance are processed via a web-enabled user interface so that the user can utilise them easily. If the data then flows into the "digital twin", the virtual image of the machine, even more precise forecasts can be made about upcoming service intervals or alarms can be programmed for deviating values. This makes holistic predictive maintenance possible.
Real-time expert support
The predictive concept is well advanced in industrial gearboxes, for example. One example of this is DriveRadar IoT Suite, the condition monitoring and predictive maintenance system from SEW Eurodrive. Among other things, modern machine learning methods can be used to provide an accurate forecast of impending damage to spur and bevel helical gearboxes. In addition to notifications when anomalies are detected during operation, forecasts are also available for the remaining service life of the drives and the lifespan of oil or components. This allows maintenance work to be planned at an early stage and spare parts to be procured in good time - for sustainable utilisation of the industrial gearbox with a minimal risk of failure.
But if it does happen, every minute counts. Remote services are playing an increasingly important role in this context, enabling faults detected by the monitoring system to be rectified remotely. With these customised support models, the service technician can use an encrypted connection to connect with the expert assigned to the machine, who can view the system in real time via a smartphone or smart glasses.