Responsibility in the Name of Water
Water has to be moved, heated, cooled and treated in order to be used. All this requires energy. According to calculations by the World Resources Institute, global water use contributes to around ten per cent of greenhouse gases. "Companies can therefore respond to the climate crisis by taking a close look at water as a vital resource," says Michael Cerilli. He is Global Vice President, Commercial Digital Solutions at Ecolab, a leading provider of sustainable water and hygiene solutions. In its studies, the company came to the conclusion that intelligent resource management in production processes can reduce water consumption by up to 44 per cent, energy consumption by up to 22 per cent and greenhouse gas emissions by up to 12 per cent. Cerilli knows: "The digitalisation of water and the analysis of the resulting data give us a more accurate picture of industrial consumption. When this information is combined with Ecolab's expertise, the use of our digital tools and automated technologies in the field enables the rapid implementation of solutions that make businesses more efficient and sustainable while maintaining profitability."
The digitalisation of water: "Ecolab Water for Climate"
The "Ecolab Water for Climate" programme is designed to support food producers in developing strategies to reduce water and energy consumption. It offers holistic solutions that include inspection, consulting, engineering, advanced chemicals and digital technologies. In addition, strategies for reducing, reusing and recycling water throughout the company are supported. Technologies based on the ECOLAB3D cloud platform are used to gain usable insights that enable rapid measures and results. These include prescriptive and predictive analyses, the digital twin and augmented and mixed reality with networked chemistry and automation. The digital ecosystem is connected to the Ecolab Global Intelligence Center. This global network connects industrial facilities and plants at six locations worldwide to experts who monitor water consumption, quality and performance in real time.
Hygienic design perfectly implemented
The economic aspect plays an important, but not the only, role in the desire to save water in the food industry. The so-called water footprint is also becoming increasingly important as an ecological seal of quality, which verifies the water consumption for the entire supply chain of a company or individual products. Carlsberg, for example, has set itself the goal of reducing its water consumption in beer production by 50 per cent by 2030. Other global players from the food industry are making similar voluntary commitments, which they intend to turn into reality - also with the help of the technologies presented at Anuga FoodTec. The goal is to reduce water consumption to the absolute minimum without neglecting the necessary hygiene.
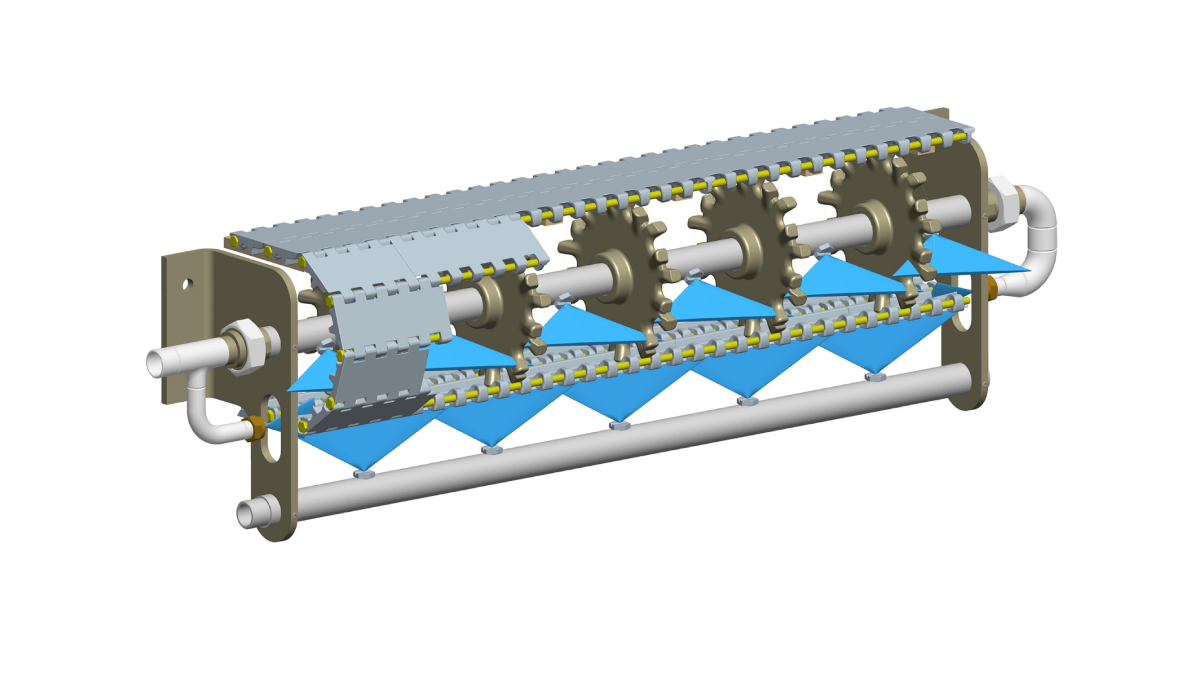
CIP system from Habasit: To guarantee the high safety standards in the food industry, conveyor belts must be thoroughly cleaned. Photo: © Habasit
The technology providers exhibiting at the Cologne exhibition centre are therefore designing their systems to be particularly easy to clean. The absence of dead corners, a straight-line design and the use of high-alloy corrosion-resistant steel with a low surface roughness prevent build-up. "Hygienic design is decisive here. Good accessibility during cleaning and the ability to dismantle parts of the machine are crucial," confirms Eric Lefebvre, Technical Manager and Managing Partner at Kronen since 2018. The HEWA 3800 helical washing machine for lettuce, vegetables, fruit and other foods is a good example of this. It's been optimised in terms of hygiene and ease of cleaning. There are no horizontal surfaces, which means that the water can drain away in the best possible way. In addition, all edges are designed to prevent the formation of biofilms. "This minimises the risk of contamination and cross-contamination. Effective access to all critical areas of the machine is also always crucial," says Lefebvre. The HEWA 3800 can be completely dismantled, enabling it to be thoroughly cleaned. Another example is the GEWA AF pre-washing machine: For quick cleaning, everything inside the wash tank is open and there's no air piping. To clean the pipe system without dismantling it and to minimise water consumption, a cleaning-in-place (CIP) system can be integrated as an option. However, the savings also relate to the chemicals and energy required for cleaning. "In addition to the fact that hygienic, safe food production must be ensured, this means a clear economic benefit for the customer," says Lefebvre.
Efficient CIP system
The criteria of hygienic design also play a key role in ensuring the clean transport of food. New here is an efficient CIP system from Habasit, which can be easily installed as a plug-and-play solution on almost all conveyor belts. A modern design supports compliance with strict food safety standards. All moving parts are carefully sealed for hygienic processes and can be monitored using inline inspection systems. The sustainable cleaning solution is also suitable for spraying cleaning agents, disinfectants and foams and contributes to reduced consumption of water and cleaning agents, resulting in cost savings in waste water treatment.
Less water for recycling
The water footprint also plays a role in answering another question: Can plastic packaging be sustainable? Astrid Kadlubski, Product Manager at the Neutraubling-based systems manufacturer Krones, explains the background: "In the recycling process, the plastics are processed into flakes using wet mills and then washed. This in turn produces wastewater in which different substances are dissolved depending on the input material." In addition to conventional contaminants, these include microplastics, organic residues from the packaging contents, cleaning agents from the washing process and printing inks removed from bottles and labels. This in turn means: The sustainability of a closed-loop technology is not only measured by the quality of its end product. The processes that lead to this end product play an equally important role. As a manufacturer of filling and packaging systems as well as recycling solutions, Krones sees it as its responsibility to fulfil both dimensions of sustainability.
Treatment of washing and milling water
The Group's MetaPure technology processes materials such as PET bottles and polyolefin packaging – in a quality that enables the recyclate to be used in a way that's equivalent to the original application. As part of the continuous optimisation of the system, Krones' developers focused on the water consumption of the washing module, among other things. This is because: "In many recycling systems, the water is recirculated and treated in a bypass," explains Kadlubski. The consequence: Contamination in the process water becomes increasingly concentrated and can ultimately affect the quality of the end product. To counteract this, Krones developed a solution for the complete treatment of the washing and milling water. According to Kadlubski, this results in several advantages: "Firstly, the need for fresh and waste water is reduced. Secondly, the recycling process runs at a consistently high level." And last but not least, the treatment process ensures that the wastewater discharged into the municipal system complies with the applicable regulations.