Measuring, controlling, regulating in the hygienic process - ifm supplies sensors for pressure and flow rate
The requirements for sensors used in the food and beverage industry are demanding. Hygienic design, a high protection class and robustness are just a few of them. The automation specialist ifm develops and produces models especially for this application. The pressure sensors of the PI1xxx series are certified according to EHEDG and FDA, among others, and fulfil protection class IP69k, so that daily cleaning with a high-pressure cleaner is no problem. The SU Puresonic flow sensor is also part of the product range. As it works with ultrasound, it does not require any disturbing installations inside the measuring tube.
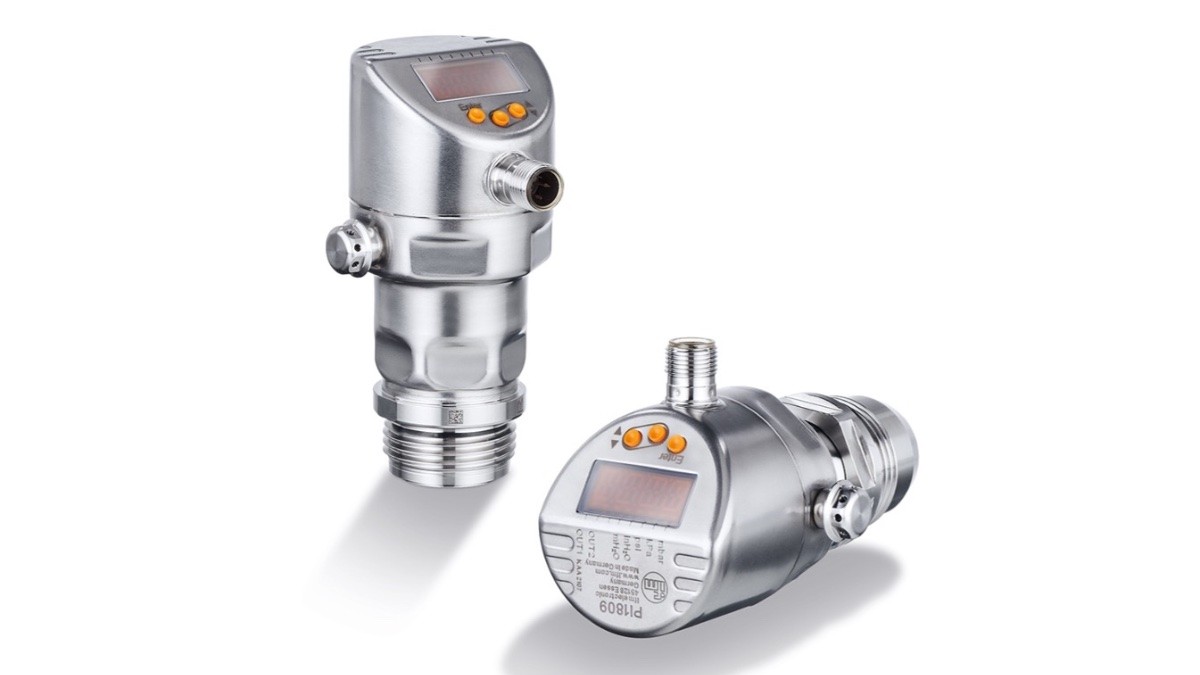
The PI1xxx pressure sensor permanently withstands media temperatures of 150 °C and is suitable for high-temperature applications in the food industry. (Photo: © ifm)
Robust communication via IO-Link
The robust pressure sensors use a capacitive ceramic measuring element. Neither abrasive or corrosive media nor vacuum or pressure peaks can damage it. In addition, the sensor permanently withstands media temperatures of 150 °C making it suitable for high-temperature applications in the food industry. The temperature can also be read out via IO-Link. The PTFE seal, which is permanently maintenance-free, also contributes to the robustness.
The pressure sensors, which are available with different measuring ranges from vacuum to 100 bar, communicate via IO-Link 1.1 and have a resolution of 32 bits. This is important for applications where differential pressures are measured and therefore only a small part of the measuring range can be used.
More convenient and therefore faster
The temperature compensation has been improved in the new series. In food industry sys-tems, the CIP process, which uses hot liquids for cleaning, is the standard. If production is then to be resumed at low temperatures, it is important that the sensor functions reliably again as quickly as possible. This has been optimised in the latest generation of the PI1xxx, so that production can restart much faster after cleaning - in many applications this leads to in-creased efficiency.
The vent opening is offset by 90 degrees on the pressure sensor and is therefore located on the side with conventional mounting. This prevents condensate from collecting on the mem-brane of the vent opening and causing contamination there. The PI1xxx has also been opti-mised in terms of user-friendliness: The operating concept with three buttons makes parame-terisation more convenient and as a result faster.
The pressure sensors of the PI1xxx series are suitable for applications in the food sector - for example in dairies, breweries and many other cases where liquids are used. Pressure measurements in these applications are carried out in tanks as well as in pipelines. Pressure measurements in these applications are carried out in tanks as well as in pipelines.
Without disturbing installations in the measuring tube
The SU Puresonic offers an optimum solution in applications where components in the meas-uring tube interfere with conventional flow sensors. Typical with flow sensors that work with moving components such as an impeller is, for example, a breakage of the blades due to po-rosity, which increases over the service life, or a blockage due to foreign bodies in the medi-um. In addition, components can be damaged during cleaning and cause the sensors to mal-function. This is different with the SU Puresonic flow sensor, which functions with ultrasonic technology. The ultrasonic transmitter and receiver are placed on the outside of the wall in such a way that the reflection occurs on the opposite inner side of the pipe. This means that no disturbing installations are necessary inside the measuring tube, which consists entirely of stainless steel.
Another advantage: The sensor does not require any seals and ensures permanent sealing. The SU Puresonic is equipped with an operating mode LED that can signal different status messages: For example, a deterioration of the signal quality due to air bubbles, particles or build-up, a failure of the electronics or a short circuit. In addition to green and red, the LED can also light up blue according to Namur NE107, indicating a change in the process.
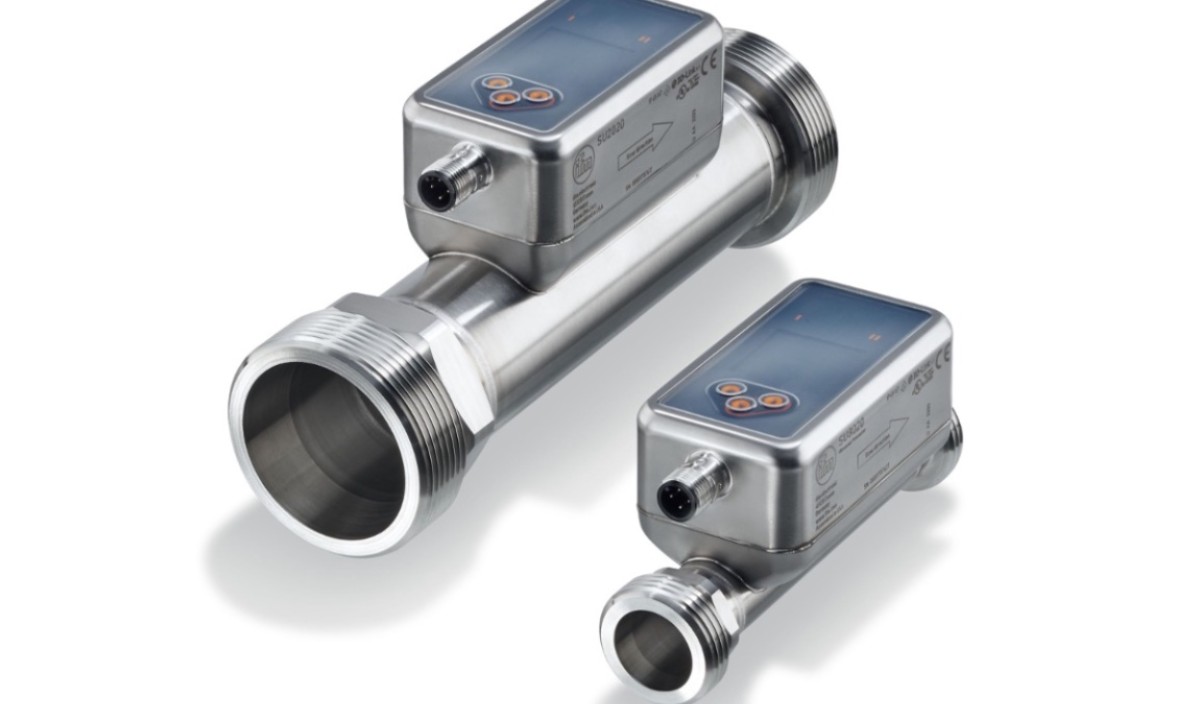
The SU Puresonic flow sensor functions with ultrasound and does not require any interfering components in the measuring tube. (Photo: © ifm)
No time-consuming selection of the right sensor
With the flow sensor, there is no need for the user to make a time-consuming selection of the appropriate sensor - for example, on the basis of the parts in contact with the medium or the sealing materials depending on the process parameters. The flow sensor is available in two sizes with process connections of one inch and two inches. The measuring ranges of the two models are 1 to 240 litres per minute and 5 to 1,000 litres per minute respectively.
Ultra-pure water, water or water-based media with an addition of additives of up to ten percent are suitable as media for the SU Puresonic. The flow sensor is mainly used in applications with pure water. Reverse osmosis, which also removes salts from the water, is usually used for this purpose.
Additional information and contact
ifm electronic gmbh
Simone Felderhoff
Tel. +49-(0)-2012422-0
presse@ifm.com
www.ifm.com