Feeding carton blanks directly from the pallet
Handling blanks with the new TLM Comfort Feeder
The background to the development of the highly innovative packaging solution TLM Comfort Feeder was the observation that delays can occur in the process if the blanks magazine on the packaging system runs empty – which result in machine operators having to react quickly to prevent unnecessary stops. With Schubert’s new TLM Comfort Feeder, this roadblock has been eliminated. All that is needed is to place the entire pallet with the blanks still in the cutting sheet into the machine. An F4 robot then pulls the blanks directly from the sheet one by one and feeds them to the erecting process in the A6 erector – at an impressive speed of 60 cycles per minute. This groundbreaking approach also offers another key advantage: The cut sheet can be optimised to ensure the greatest possible utilisation of the packaging material. This saves on material and has a positive impact on the ecological footprint. The combination of innovative sheet feeding, outstanding erecting performance along with loading and sealing offers Schubert customers an exceptionally advantageous machine concept. The bar packer is part of Schubert’s TLM Power Compact machine category, which describes TLM machines that deliver a high output density in a small space.
Schubert’s extensive technology portfolio meets the most diverse needs
From pick & place robots in the Pickerline to Flowpackers and Casepackers, all the way through to complete packaging lines, Schubert is ideally positioned to provide all the technologies that food manufacturers need to achieve high-quality packaging. Furthermore, Schubert’s flexible, modular and easily convertible packaging machines process both conventional and fully recyclable packaging. Martin Sauter, Head of Sales at Schubert, explains: “As a packaging machine manufacturer, sustainability is extremely important to us. This is why we are continuously developing our innovative packaging machines towards achieving this overarching goal. Last year, for example, we also equipped our Flowpacker with Box Motion sealing technology, which enables cross-sealing using ultrasound. The seal is also perfectly suited for recyclable flowpacks made from monofilms or paper-based films.”
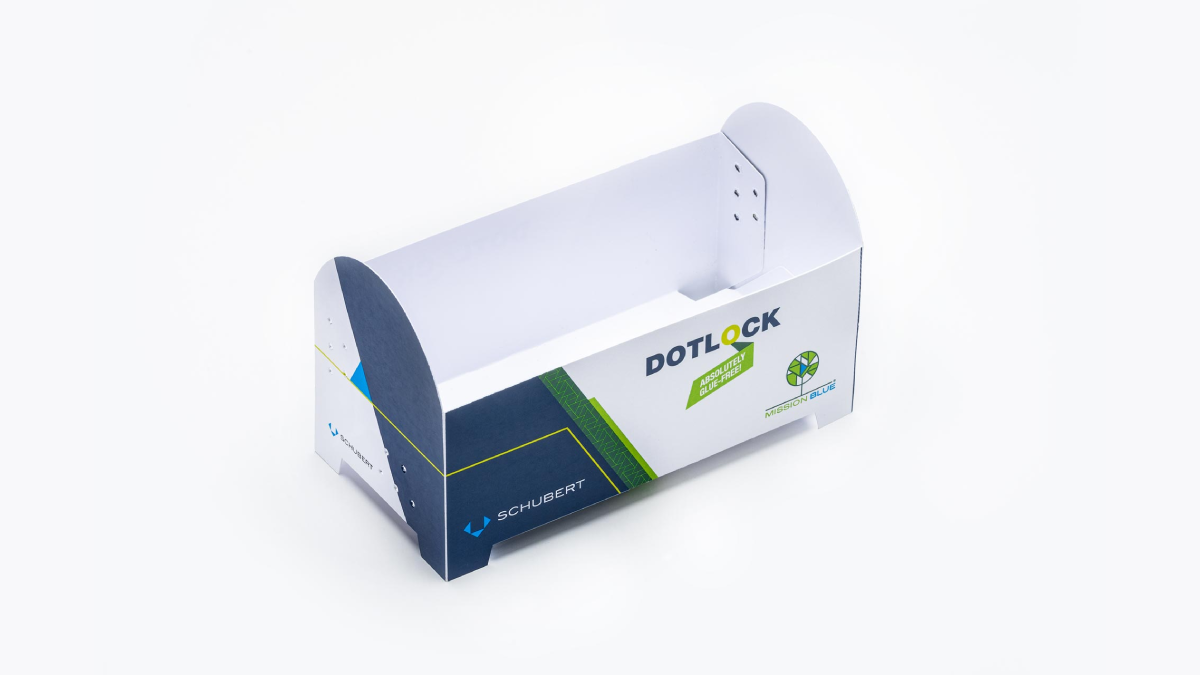
Dotlock is a 100 per cent glue-free technology for carton packaging – developed in-house by Schubert.©Gerhard Schubert GmbH
Cardboard packaging without glue and a hybrid solution with extremely thin film
With Dotlock, Schubert has developed a technology that makes cardboard packaging entirely glue-free. Dotlock is based on so-called “clinching” technology used to join metals. The cardboard layers are pierced from one side with a needle, forming a collar on the other side. This is then pressed onto the cardboard, creating a very stable force & form fit. As a 100 per cent glue-free packaging solution, Dotlock is fully recyclable via the paper cycle. The new hybrid packaging consists only of cardboard and very thin monofilm, both of which are very easy to separate and therefore fully recyclable. Martin Sauter explains: “Our focus is on modular, digital, robot-based packaging machines and lines. But we are also involved in the development of sustainable packaging processes on a selective basis. Samples of both Dotlock and the new hybrid packaging can be viewed at our stand.”
Further information: www.schubert.group