Integrated planning for buildings and processes
Into the future with energy efficiency? Industrial building expert Tobias Rosenbaum is convinced that, with the right strategy, food producers have great opportunities for leveraging cost potentials and optimising their operations at the same time – “provided that processes and buildings are regarded as a system when planning measures”, as the managing director of IE Food Munich explains in the interview.
Mr Rosenbaum, what does IE Food stand for and in which sectors does your company operate?
Tobias Rosenbaum: IE Food plans, designs and constructs industrial buildings for the food industry. Our top priority is to ensure the maximum possible efficiency in production with the aid of solutions that are coordinated to our customer’s individual production processes. No matter whether new builds or extensions to an existing plant are involved, the end result is sustainable industrial buildings that are efficient, low in emissions and flexibly usable.
Above all, the changes in value chains, the energy crisis and the resulting shortage of resources are compelling companies to rethink things. Are these also the requirements with which food producers approach you?
Yes, the energy crisis is becoming a permanent state of affairs and necessitates radical measures to maintain companies’ competitiveness. However, our customers are usually concerned with extending their production capacities and optimising their processes. New plants and buildings are needed, for example, or they are considering building a high-bay warehouse with picking and corresponding temperature zones. Production extensions are then often the starting point for transforming an entire site’s energy supply, however, and making it fit for the future.
… So redevelopments and modernisations in existing buildings offer the potential for increased energy efficiency?
Extending the production or logistics facilities often gives rise to new potential for lowering operating costs in the long term, particularly in existing buildings. In this context, energy efficiency in existing buildings with poorly insulated envelopes and obsolete energy production systems and infrastructure plays a particularly important role. Experience has shown that cost savings of between 20 and 50 percent are possible in such old buildings depending on the food segment and manufacturing processes. However, looking at buildings holistically in conjunction with the production processes and the plant technology is of elementary importance for reducing CO2 emissions and energy costs. Only then can the potentials be leveraged to their full extent.
How do you assess the state of the building technology within the companies under the aspect of energy efficiency?
Naturally, the core production processes are the primary focus of most companies’ efforts. Extending the product range and intralogistics are often the biggest drivers of investments for the companies. Conversely, the building and infrastructure side of things is often neglected. On the whole, it has to be said that old structures and sites are frequently hung on to for too long. If production plants have been planned in isolation and sometimes literally squeezed into existing buildings, innovative approaches that are significantly more cost-effective are missed out on.
What is your approach to planning?
The starting point is always a holistic analysis of the actual situation, because the resulting tasks differ extensively from company to company. Depending on the company’s objectives, we then develop the projects in terms of feasibilities and master plans with a medium- to long-term horizon. To do this, we use an integrated planning method in which architects and engineers develop the projects together on the basis of operations, process and logistics planning.
Energy consumption in the food industry is extensively influenced by the provision of heat and chilling for processes. In many places, however, large parts of the primary energy are transformed into waste heat, and many people are likely to be unaware of just how much energy is lost as a result. What are the options available to producers for making waste heat usable?
First of all, it is important to critically analyse the primary process heat requirements: many steam-heated processes could be switched to hot water. Or the cooling medium can be ambient air or less extensively cooled air instead of wasting more expensive industrial refrigeration for this. While this influences the plant technology due to the increased size of heat exchangers or the bigger area needed for cooling zones, it is the prerequisite for the next steps, such as local sector coupling within the company, for instance.
… meaning?
Energy systems and the heat supply are being increasingly electrified. Heat pumps convert electricity into heat, but also function the other way around under certain circumstances, meaning that waste process heat can be converted into electricity. Often, this waste process heat can be used to heat the building including the administrative tract or the social facilities. However, potential is also offered by incorporating the company’s surroundings and neighbourhood into the energy concept. This can include outputting heat to external consumers such as the community’s district heating network, for instance. Even temporarily buffering surplus energy can often prove advantageous.
When is it sensible to involve the use of renewable energies?
Essentially, renewable energies should always be integrated into the energy concept; of course, this is mandatory for extensions and new builds. In some German federal states, it is actually already set down in law and is the prerequisite for obtaining planning permission. The situation differs from company to company depending on the production process. It is important to analyse the internal energy consumption over a long period of time, meaning that production and shift models as well as seasonal fluctuations over the year also have to be factored in.
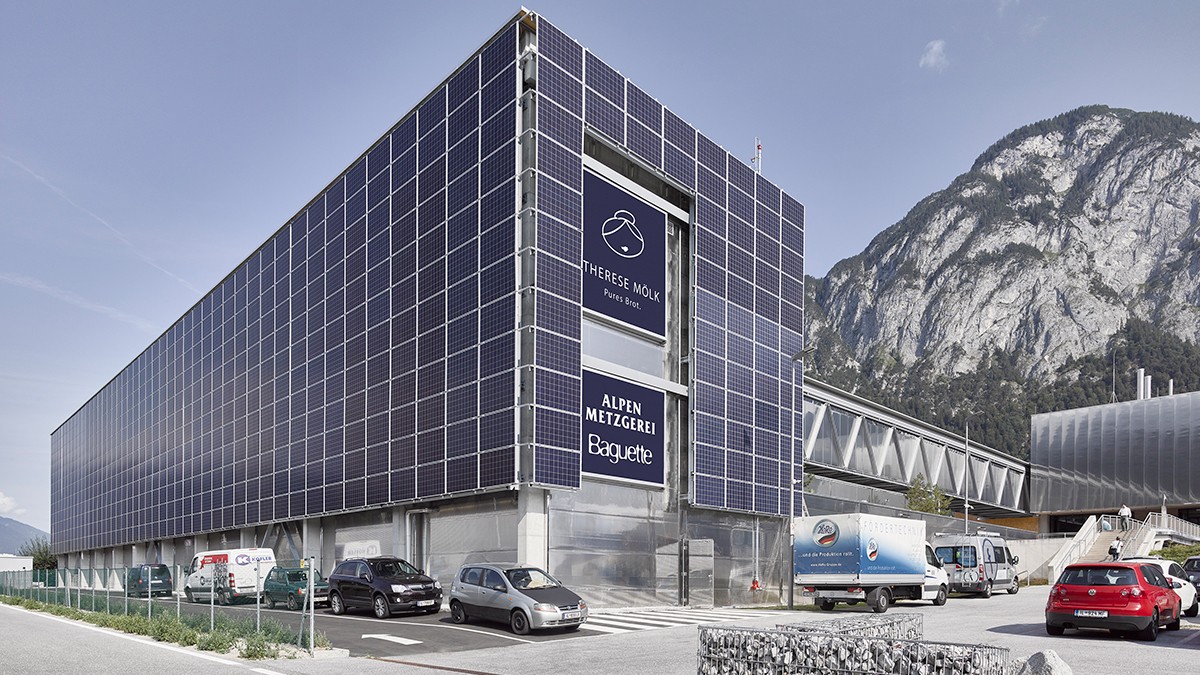
… Presumably it is always a mix of different regenerative energies that leads to energy self-sufficient, CO2-neutral production.
Planning for integration into the building right from the outset is important. High energy self-sufficiency can be supported well with photovoltaics in companies with high electricity consumption, for example. Sector coupling – PV electricity with cooling – is appropriate for a refrigerated or deep-freeze warehouse, for example: the more sunlight that heats the building, the more electricity needed for cooling is produced. Geothermal energy or ambient media such as air and water as energy sources in combination with heat pumps improve the economy of consistent thermal processes. Essentially, short distances with low losses caused by conversion and storage should always be sought.
Added to this is the fact that whoever wants to innovate also has to invest. Are there any subsidy programmes that are currently available for this?
Firstly, there are the familiar subsidy programmes for energy-efficient buildings from KfW and secondly, the subsidy programmes offered by the Federal Office for Economic Affairs and Export Control (BAFA). In particular, innovations in the area of energy-efficient processes and production techniques are subsidised via various programmes at national and federal state level. However, the subsidy conditions change constantly and are subject to political will. It is therefore important for investors to constantly keep an eye on the subsidies and to be willing and courageous enough to react at short notice. The EU taxonomy, ESG reporting and higher CO2 certificate costs in the future are putting additional pressure on companies to make themselves more sustainable and energy-efficient.
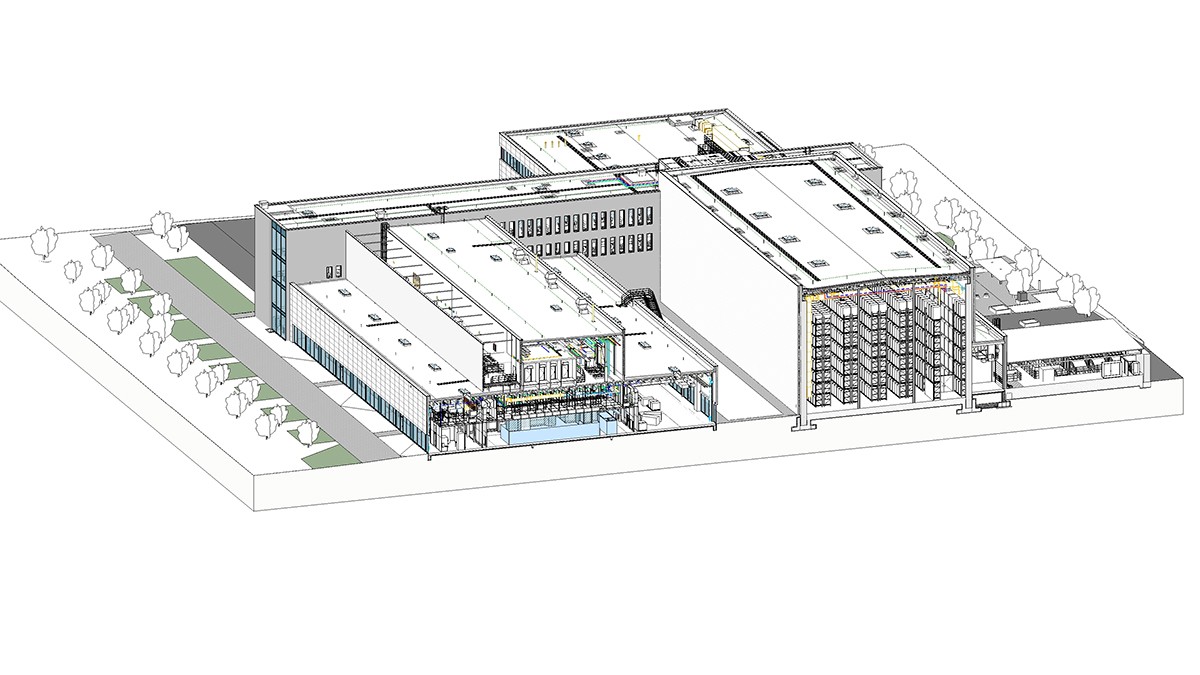
About IE Food
IE Food is a division of the IE Group and offers operational and construction planning for complex and demanding industrial construction projects from a single source, for both new builds and extensions to an existing plant. The Group, which has been on the market since 1966, currently employs around 100 staff. Business and mechanical engineers, logistics and construction specialists as well as architects work at the company’s sites in Zurich, Munich and Lausanne.