Invisible Top Performance
Country-specific material approvals
Many systems are usually cleaned and sterilised while closed to maximise system effectiveness. However, this requires the seals to be highly resistant to the acids, caustic solutions and disinfection media used in the process, such as peroxides or chlorine. In addition, country-specific and consequently widely varying material approvals and material conformities must be fulfilled.
In addition, the market is very dynamic: The range of food and beverages offered is constantly changing. The regional differences are considerable. In turn, the processing companies - and before them the machine and system manufacturers - are reacting to this. They benefit from close cooperation with the seal manufacturer: Both combine their market knowledge and jointly identify current developments in the food and beverage industry. Some examples of current challenges in the industry are described in the following.
Greater product diversity
New foods and beverages are becoming established. Milk alternatives, for example, have conquered part of the market. However, products such as soy, oat or almond milk place different demands on the processing systems. For example, they contain other fats, and abrasive substances such as almond shells or oat bran increase wear. A look at beverages with two examples: Flavoured mineral waters are becoming increasingly popular, and breweries don't just produce traditional beers. This diversity places demands on the seals: They must be closely matched in material and design to the other substances processed or must cover a wider spectrum. In addition, they must not promote aroma transfer when different products are produced with one machine or system. If contract filling companies are involved, all quality standards naturally apply there as well.
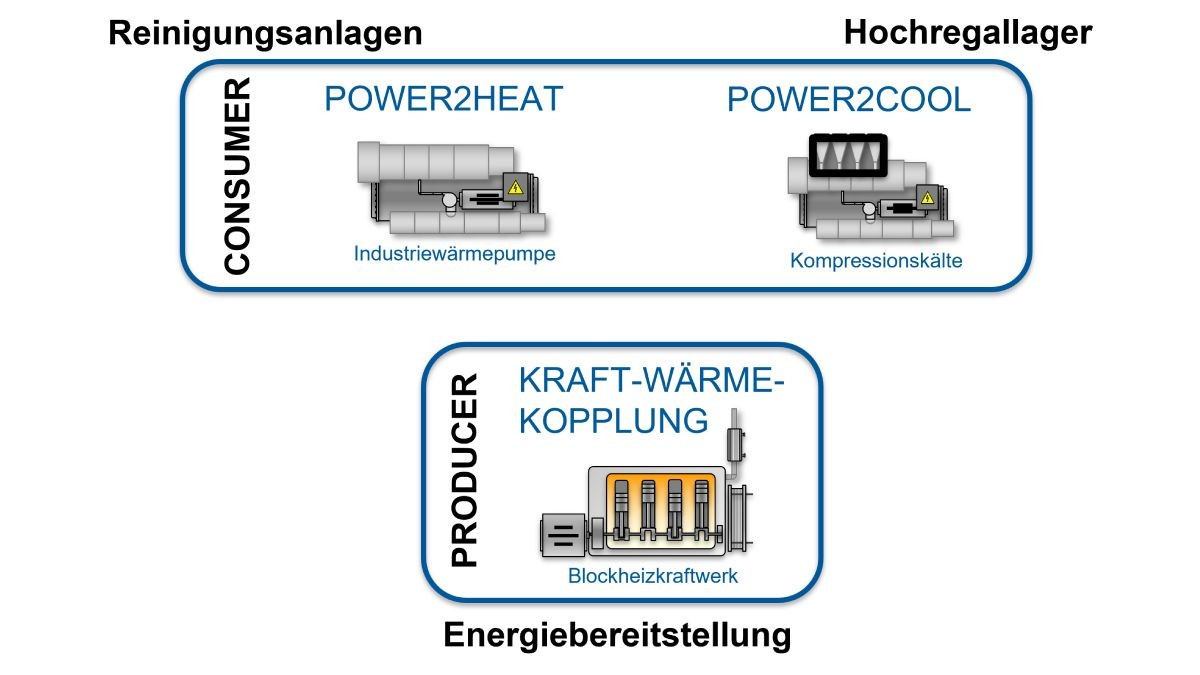
Common material variants compared with Fluoroprene® XP ©Freudenberg Sealing Technologies
Hygienic design
A basic prerequisite for sealing solutions according to "hygienic design" is a design free of dead space, closely oriented to the intended application and system. The FEM (finite element method), improved with special material models for elastomers, is of major importance here. A seal designed using this method promotes optimum flushing, thereby preventing, for example, product residues and microorganisms from collecting and settling in undercuts. Even under temperature, dead spaces must not occur due to deformation. And the selection of the materials used and their resistance to hot water, steam flushing systems, acids and caustic solutions is also relevant - even at increased concentrations, pressures and temperatures. It is therefore advantageous if the seal manufacturer offers its own material development for high-performance plastics and elastomers. Elastomer and PTFE materials comply with the standards and are also resistant to CIP/SIP (Cleaning in Place/Sterilisation in Place) media.
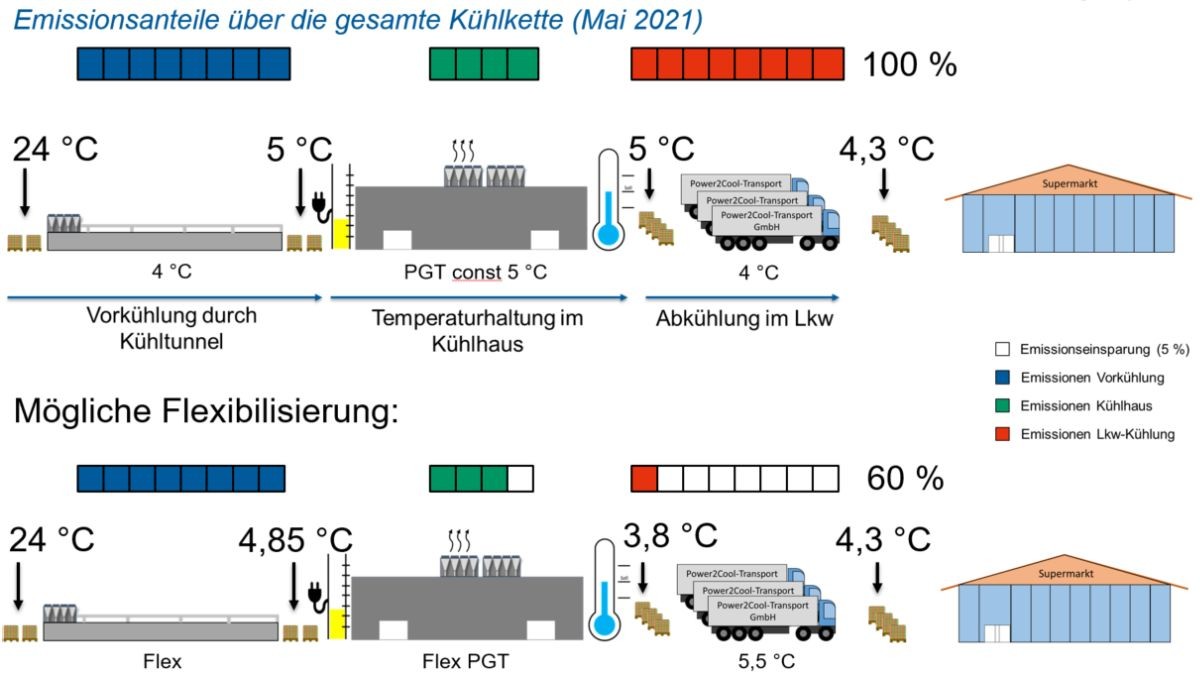
Example of dead space - standard vs. hygienic design ©Freudenberg Sealing Technologies
Increasing production output
Only properly functioning machines and systems can run at full capacity and produce the desired yield. Innovative seals are designed for this: Their service life and full functionality usually correspond at least to the maintenance cycles. In addition, they significantly reduce friction. These and other factors also require know-how in material selection and design. The latest calculation and testing methods predict the service life. A recent development for digitalised systems and complex applications are "smart seals", which provide information during operation about their wear, for example, in addition to their actual sealing task. This allows maintenance cycles to be planned well in advance.
Seals are answers to customer requirements
Seals occupy a comparatively small space in a machine or system and its investment volume. In view of the diverse and extensive requirements, an increasing number of companies nevertheless appreciate close communication with the seal manufacturer and its material and technical expertise. This is because more and more frequently, system engineers are not resorting to standard gaskets, but are specifically looking for an individual combination of the seal material and design. Sometimes this delves deeply into the fundamentals of materials science. Rapid prototype production, such as with Freudenberg Xpress®, complements the range of products and services offered. For many aspects of cooperation, an accredited laboratory and in-house test benches are also essential. In turn these provide well-founded answers to practical applications and materials.
High delivery capacity
Whether for the construction of new machines and systems, regular maintenance or a repair: Seals must be available. In times of widespread supply bottlenecks, exemplary delivery capacity becomes even more important. The corresponding service orientation begins with high-performance production within reach. Extensive stocking and a customer-specific logistics strategy are further building blocks for ensuring that the seal is delivered promptly to destinations all over the world.
Zukunftsorientierte Vernetzung
The dynamics in the food and beverage industry make it necessary to constantly be in touch with the times. In addition to close contact with the customer, this also includes the seal manufacturer's participation in regulatory bodies, which enables it to help shape important framework conditions. Bute the view ahead reaches even further: Cooperation with universities and participation in research projects provides insights into the technologies, materials and processes that will be in demand in the future. Combined with the company's own expertise, developments can be thought out in advance and, ideally, the seal manufacturer will already have the right product ready when a machine or system manufacturer comes forward with a task.
Freudenberg Sealing Technologies
Mobil + 49 (0) 6201 - 960-66 66
Write an e-mail