KUKA hygienic oil portfolio increases food safety
One in eight food products is contaminated with mineral oil residues that can be harmful to health. This was the result of a foodwatch analysis of more than 150 products in various European countries in 2021. The dangerous contaminations happen partially in the automated production and packaging process, but those can be completely prevented with the right technology. Industries such as the medical, pharmaceutical and food industry have a zero percent tolerance for contamination and require plant manufacturers to use so-called NSF H1 lubricants. KUKA has launched a complete HO portfolio with robots that meet these stringent requirements.
All axles with food-grade lubricants
For machines used in these industries, this means in concrete terms that they must be designed and built in a way that prevents operating fluids that are hazardous to health, including lubricants, from getting in touch with the products. If some lubricant leaks, it must be composed in a non-toxic, harmless way and, of course, shouldn’t affect the taste of the product. “As KUKA, we take this very seriously, especially since our robots are increasingly used in these fields,” explains Dieter Rothenfußer, portfolio manager at KUKA. “All axes of our HO robots are therefore equipped with food-grade lubricants, as is the energy supply system to the robot tool.” This makes consistent NSF H1 lubrication of the HO portfolio possible along the entire process chain – not only in production machines and conveyor systems, but also in the robot. The U.S. National Sanitation Foundation (NSF) checks whether the lubricants are compatible with foodstuffs and grants them H1 approval, i.e. food approval. This means that if a lubricant from an HO robot comes into contact with food or pharmaceuticals – for example, after a malfunction of the robot or if oil vapors escape from the machine due to compressed air – this is harmless to consumers.
This means that KUKA's entire HO portfolio meets the necessary hygiene requirements in accordance with the Machinery Directive 2006/42/EC as well as DIN ISO 14159. These regulations additionally state that machines must be designed, built and installed in such a way that the ingress of operating materials such as lubricants, hydraulic fluids and signal-transmitting liquids into the product must be prevented. Another plus is the “HO” identification as a food robot, which is visible from the outside. Any errors during maintenance – for example, the use of standard oil – are thus easily avoided.
_m24_full_m36_1025.jpg)
Hygiene along the entire process chain: the new KR IONTEC HO completes KUKA's powerful, versatile HO portfolio.
New KR IONTEC HO completes the family
There’s good news for all entrepreneurs in the food and pharmaceutical industries who are planning to automate: the range of Hygienic Oil robots from KUKA is growing. Three hygienic variants of the KR IONTEC have now been launched on the market. They complete the portfolio, which previously consisted of corresponding variants of the KR QUANTEC, KR CYBERTECH, KR AGILUS and KR DELTA. With a new, sealed stainless steel flange and even hygienic oil of an even higher quality, the new version offers strong support, particularly in the food sector. With a payload of 50 to 70 kilograms and a reach of between 2101 and 2501 millimeters, it finds numerous areas of application. “In cheese processing in particular, many of our customers have been waiting for this new robot variant," reports Rothenfußer. The new KR IONTEC impresses with a dirt-repellent, highly corrosion-resistant surface of category C4, in accordance with DIN EN ISO 12944-2:2018-04. In addition, even the energy supply system for the respective robot tool is available with HO cable greasing. In addition, customers benefit from the fundamental advantages of the KR IONTEC: it has low energy consumption, low operating costs, can be flexibly installed, and its particularly slender design also qualifies it for production environments with little space.
Hygiene measures also elementary in the packaging process
The hygienic work of the robots is also becoming increasingly important because more and more countries are giving up plastic and machines therefore come into contact with food during packaging and palletizing. The EU has set itself the goal of reducing packaging waste by 15 percent by 2040 compared to 2018. France, for example, did away with packaging certain fruits and vegetables in plastic in 2022, and as soon as 2026, all fruit and vegetables are supposed to be sold without any plastic wrapping. It is not only the workers who are packaging cucumbers or apples, for example, who then have to be careful to protect foodstuff from contamination. Even one step before, caution is required. This is because foreign substances on packaging, such as cartons or foil, can also diffuse inside, contaminate food and result in expensive recalls. For this reason, the supplier industry for food packaging is also showing increasing interest in HO robots.
The EU Food Hygiene Regulation also obliges all food producers to analyze the individual production steps and install a preventive control system called HACCP (Hazard Analysis and Critical Control Points). It aims at ensuring the highest possible level of food safety. In this context, the use of H1 lubricants along the entire process chain is explicitly pointed out.
The food industry has recognized the need for automation years ago. As early as 2021, the number of robots used in the food and beverage industry worldwide rose by 24 percent to around 15,300 systems. And the trend is continuing. Whether handling, packaging or palletizing: KUKA's portfolio can cover the entire production value chain. This is also ensured by the KR AGILUS HM and KR DELTA HM hygienic machine (HM) robots. They were developed for applications involving raw foods and pharmaceuticals. In addition, the KR QUANTEC PA palletizing robot, which is also available in a hygienic version, has long proven its worth in the food sector. For handling frozen goods, there is also an Arctic variant which can withstand temperatures as low as minus 30 degrees Celsius without a protective cover.
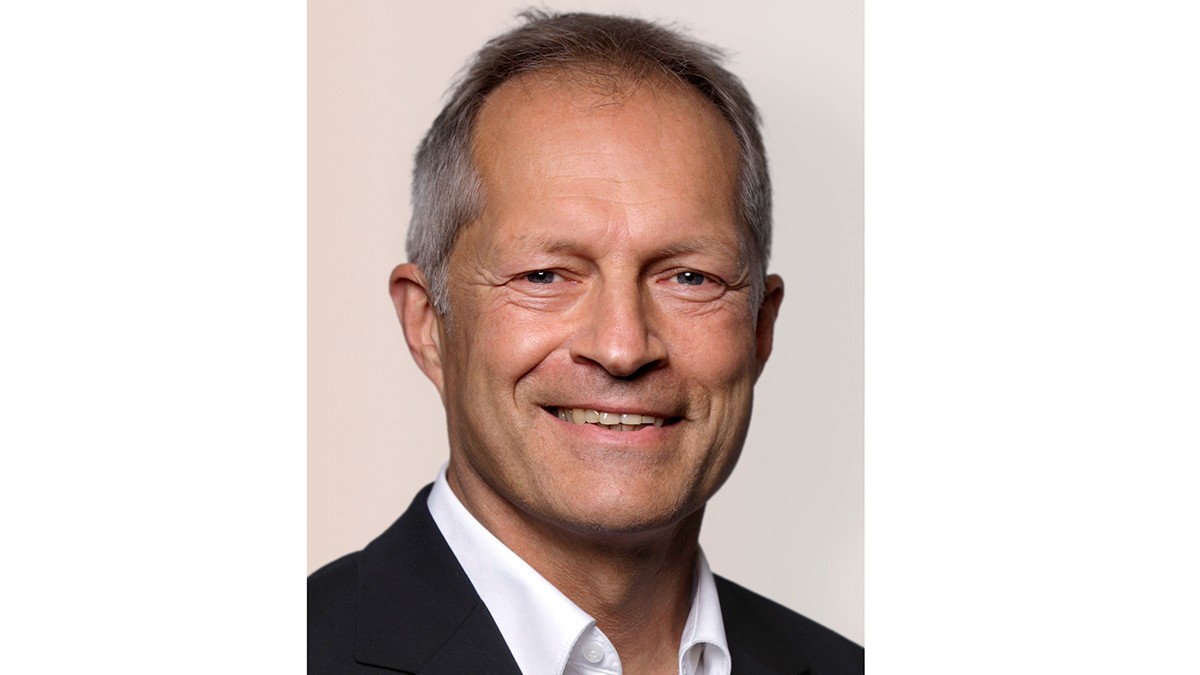
“Thanks to the expanded HO product line from KUKA, we can meet the needs of our customers in the food sector even better with our customized special machines.” Marc Winkelmann, CEO Robofact AG
KUKA.PalletTech simplifies palletizing applications
The KUKA.PalletTech software is particularly suitable for tasks in mono-palletizing, where it offers maximum efficiency with very high flexibility. Whether single-pick and single-place or single-pick and multi-place: the software can be used to simplify a wide variety of palletizing processes with all five-axis and six-axis robots from KUKA. This also includes the new KR IONTEC HO.
When it comes to automation in industries such as food or pharmaceuticals, software such as KUKA.PalletTech and food-grade oils are crucial success factors. They enable the requirements for hygiene, speed and flexibility to be met – everything from a single source. Food contamination, as discovered by foodwatch in numerous European countries, can thus be completely avoided.