Optical foreign object detection made of plastic
Foreign objects like blue plastic splinters must not enter food products. To ensure that only flawless items reach the market, manufacturers need to inspect each individual package. CLK has developed the MultiCheck for this purpose, which is used in multi-head weighers to control the product flow. Unlike X-ray and metal detection methods, the optical camera system recognizes contaminants based on their color through image processing. This system provides an optimal complement to the other two concepts for foreign object detection because no single system, especially not visual inspection by employees, can offer 100% certainty.
The idea for the MultiCheck arose from a request within the food industry. A customer was looking for a way to inspect food for foreign objects during the portioning process. "Portioning typically involves the use of multi-head weighers," explains CLK owner and CEO, Dr. Carsten Cruse. "The circular system is self-contained, and it's not easy to search for foreign objects within bulk material during weighing."
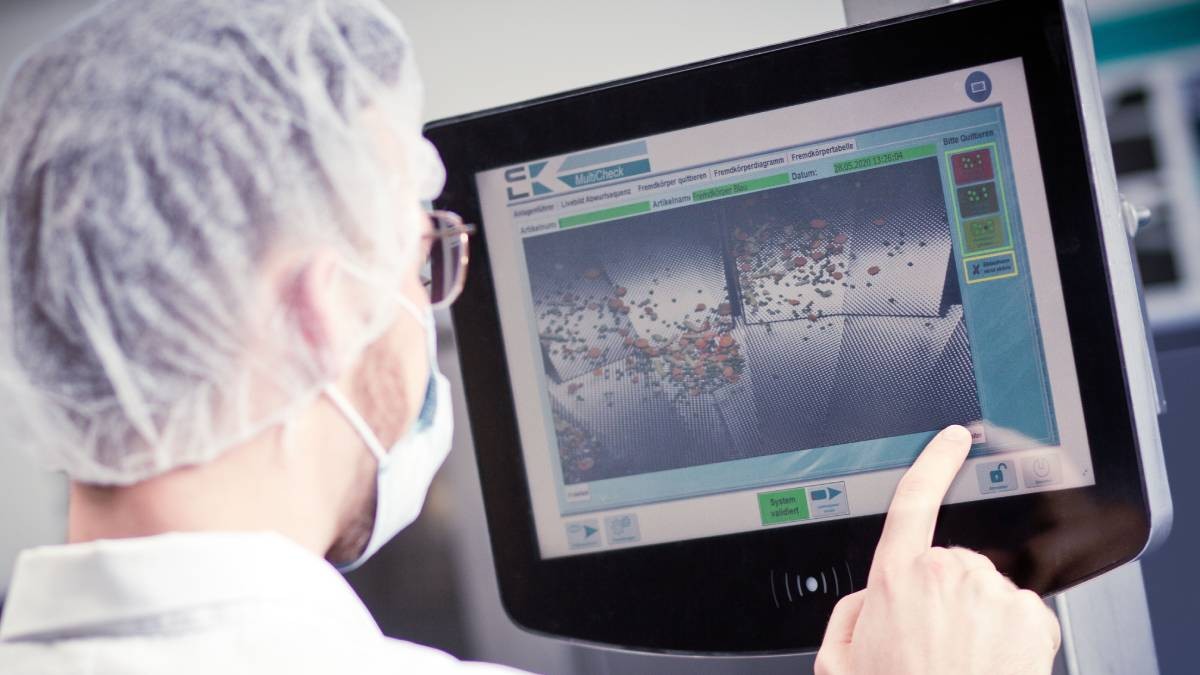
The MultiCheck
The compact camera system, the MultiCheck, is placed within the multi-head weigher. Mounted at the upper end of the discharge chute, it provides the best and longest view of the falling product without making physical contact. As soon as the multi-head weigher dispenses a quantity of product, the MultiCheck receives a signal triggering the capture of a sequence of images. Four cameras allow for a 360-degree panoramic view with no blind spots, capturing images from different angles simultaneously. If the system detects a foreign object made of plastic or other materials based on its color within the product flow, it generates a signal to halt the equipment or, optionally, to eject the affected portions. Conducting foreign object inspection as the final step before packaging ensures high safety standards.
(Zwischen-Headline 2) Simple Retrofitting
Existing multi-head weighers in production can be easily retrofitted with the MultiCheck. It also functions reliably when there are changes in the product. With the information about the number and type of contaminants detected, food manufacturers can identify faulty processes in production. This patented and award-winning MultiCheck contributes to enhancing the competitiveness of the companies.
Simple Retrofitting
Existing multi-head weighers in production can be easily retrofitted with the MultiCheck. It also functions reliably when there are changes in the product. With the information about the number and type of contaminants detected, food manufacturers can identify faulty processes in production. This patented and award-winning MultiCheck contributes to enhancing the competitiveness of the companies.
_1200x675_m24_full_m36_1025.jpg)
Food Extruder in Hybrid-Version wie der ZSK von Coperion ermöglichen es Herstellern, schnell zwischen der TVP- und HMMA-Produktion zu wechseln. Copyright: Coperion
The VacuCheck
Vacuum-sealed cheese sachets provide optimal protection and are used wherever long-term freshness and food quality are crucial. If these packages are not completely airtight, there's a risk to the product's quality and safety, potentially leading to costly recall actions. To reliably detect packaging defects and sort out faulty bags, food manufacturers rely on precise inspection systems. Fully automated and integrated into the packaging line, the CLK VacuCheck takes on this task. Depending on the hardware used, its powerful software offers a high detection rate of over 70 products per minute.
Thanks to state-of-the-art camera technology and AI-powered image processing, the CLK VacuCheck identifies nearly 100 percent of all faulty packages. This is done fully automatically in the packaging line, adhering to the criteria of Hygienic Design. The VacuCheck, placed directly above the conveyor belt, ensures the inspection of all products.
The principle
Thanks to the integrated cameras, the packaging is analyzed and identified by a rapidly learning algorithm. A tight vacuum bag exhibits a characteristic pattern on its surface, whereas a leaky one does not. If the image recognition detects a deviation from the defined target state, this information is transmitted within the system, and the faulty packaging is automatically rejected. The advantage of the CLK VacuCheck is that it operates in-line over an existing conveyor, making it suitable for high production line speeds.
Digital Documentation of Inspection Processes
Every result of the optical inspection, followed by evaluation through the software, is stored in an internal database. By utilizing flexible hardware and software, we can easily adapt our systems to the users' needs or change requests. We also offer optical leak testing for Euroblocks following a similar principle. It offers the same advantages as the standard version. It's also possible to combine both inspections in a single system.
Kontakt
Katja Opitz
CLK GmbH, Altenberge
Tel. +49 2505 93620-44
info@clkgmbh.de
www.clkgmbh.de