Recyclability
Mr Désilets, what do you think are the best approaches to designing packaging sustainably and making it fit for the future?
Sustainable packaging takes a different form for every company and is individually tailored to the company’s needs. We therefore recommend that each company first take stock of the status quo in a holistic sense. That then also includes the entire supply chain process and the internal procedures.
What are relevant, sustainable materials for food packaging? Which can be recycled very well? In which do foreign materials such as adhesives, printing inks/lacquers and additives pose a particular challenge?
All materials can per se be processed to manufacture sustainable food packaging, but I can also develop poor options from all of these materials.
Let’s take plastics, which are having a hard time in our present disposal infrastructures. Even plastics that can be recycled very well in theory are often only reprocessed to form recyclate to a minor extent. That starts with collection in the household and is similar to a lottery: if you don’t play, you can’t possibly win. However, I can also use plastics to produce very nice reusable containers, whether they be drinks bottles, to-go crockery or containers for my ‘unpackaged’ shopping.
Almost all materials are recyclable in general, but focus is placed above all on the common, widespread and sought-after materials such as polypropylene, polyethylene or PET in the case of plastics, and of course fibre packaging made of paper and cardboard – which have a recycling rate of over 90% – metals, and aluminium and glass. On the one hand, that has to do with the material itself, which can be easily sorted and recycled back to its original form. On the other hand, simple collection of the packaging is a very important factor. Virtually every household has a paper bin outside, but far fewer have a bin for plastics. Glass is also readily collected and disposed of, something that is presumably learnt and also due to the good image that glass has as a sustainable material. Perhaps the consumer pays more attention to correct disposal with ‘sustainable’ packaging?
Why can lacquers/printing inks, adhesives and other additives prove challenging?
Additives and printing inks, etc. play a role in all materials. They usually lead to the contamination of the recyclate and therefore to reductions in quality or volumes. The wrong additives, adhesives and lacquers can actually hinder or significantly reduce recycling, particularly in the case of plastic and paper/cardboard. This is one of the reasons why we are increasingly focusing on the ‘minor’ players in the packaging in new concepts, because they are more relevant than is generally assumed.
How do foreign materials such as adhesives, printing inks/lacquers and additives influence the quality of plastic recyclates?
Nowadays, plastics are usually distinguished using near infrared scanning (NIR) in the sorting plant – at least where smaller packaging is concerned. NIR is reliant on the packaging material being ‘visible’ so that it can be identified correctly. A dark colour that is based almost 100% on carbon black hinders this visibility and therefore makes clear identification of the material impossible. These materials and packaging are then discharged and burnt. The darker the design of the packaging – with a dark plastic as the material as well, for instance – the more difficult it is to identify the material.
However, printing inks, adhesives, lacquers and additives also have a negative impact in the next process: during recycling, the plastics are melted again at high temperatures. If the foreign substances cannot withstand these high temperatures of 230-250°C, they evaporate or are gasified. This results in high pressure in the extruder, which places strain on the machine. It also leads to odours and vapours, some of which are unhealthy and some of which impair the food. This is why heat-resistant foreign substances should be used in plastics. While they impair the recyclate, they at least do not outgas and produce any odours.
What are the first steps for improving the recyclability of conventional plastic packaging? What should be taken into account when designing the packaging?
We always think about recyclability from the end-of-life scenario, i.e. the likelihood with which certain conditions will occur. Let’s assume that packaging is sold in Germany. From our perspective, we should then primarily encourage consumers to put their packaging in the yellow bag or bin – back to the lottery scenario again. The amount of additional recycling potential that remains unused here alone is around 50%.
Then, the packaging should be designed on the basis of materials that are also sorted and recycled: at the moment, these are essentially polypropylene (PP), polyethylene in low-density (LDPE – such as flexible films) and high-density form (HDPE – such as solid shampoo bottles, for instance). Classic yoghurt pots made of polystyrene (PS) are only rarely used nowadays and are therefore not always sorted, because the margins are unprofitable. PET is pretty much not sorted at all, although efforts are being made. This is why what marketing departments hail as ‘sustainable’ PET containers made of recyclate are also extensively doomed to be burnt at the sorting plant. We advise against using PET recyclate from the PET drinks bottle stream, because it interrupts the closed PET cycle.
Attention should also be paid to the most uniform plastics possible, and a mix of different plastics should be forgone. Packaging made of PP or PE with an EVOH or PVOH barrier layer is easier to recycle than multi-layer packaging made of various layers of different plastics. The metallisation of plastics is also questionable, whereas thin aluminium or SiOx vapour deposition is relatively unproblematic in sorting. There are numerous parameters that have to be considered. We drew up a guideline for this back in 2018 even before the packaging legislation came into effect.
Which are the most frequent foreign substances? How can foreign substances be avoided through the design of packaging?
Besides the printing inks, additives or adhesives, common foreign substances also include metallisation for forming barriers against oxygen, water vapour, greases and oils. Finishing lacquers such as UV lacquer, gloss and matt lacquers are pretty much standard for packaging. As a rule, the cheaper ones are also more harmful for recycling. Unfortunately, the majority of purchasers and packaging developers aren’t aware of that.
Why can odours develop in recyclates? Where do they come from? How can they be avoided?
Odours in recyclates stem from the gasification of foreign substances in the extruder. They are gasified at the high temperatures and the contents, some of which are also toxic, escape from the plastic. PVC or PVDC are certainly some of the foreign substances that not only produce toxic substances during manufacturing, but also during recycling. This is why they are increasingly being avoided. The Healthy Printing initiative, which has already been around for a number of years and of which pacoon is also a member, makes sure that healthy constituents and printing inks are used in production and processing.
Why are adhesives, printing inks and lacquers challenging in paper recycling?
They play more of an important role in the paper recycling process than in the sorting process for the numerous paper and cardboard qualities. A few basic rules have to be observed in this case: the fibres are not chopped or cut during recycling. While the packaging is torn into smaller, manageable pieces, the fibres are not cut. The University of Graz, for instance, has already determined that the fibres per se are not shortened during recycling, but that the fibre thickness is reduced over time.
In the first step, it is important to make sure that the fibres are not given a waterproof coating on both sides so that water can reach the fibres and detach them from any films, printing ink particles or pigments. Printing inks and lacquers are then cleaned from the fibres in several process steps. However, this only really proves successful if the foreign substances are not water-soluble. Water-soluble materials are then filtered out along with the fibres, can clump together again later on during drying and can contaminate the fibres or discolour them and reduce the recycling quality. Over time, the foreign substances can also accumulate again in the water and then become deposited in the paper, which can in turn lead to tearing during paper production. Particles that are not water-soluble and which are separated from the fibres should therefore be selected.
How can the design of paper packaging be optimised for recycling?
First and foremost, the packaging should meet the requirements of the product. For food, these usually include barriers, which the paper rarely offers by itself. However, new developments are shifting towards the additional application of these barriers, such as grease, oil, oxygen or water vapour barriers, for instance. It has to be ensured that recycling remains possible in this case. Such composite paper or fibre packaging usually consists of 70 to 90% fibres that can be easily recovered if the packaging has been designed correctly. The automatic separability of different materials – as with the famous ‘K3’ cup, for instance – makes it easier to recycle the individual materials in composite packaging.
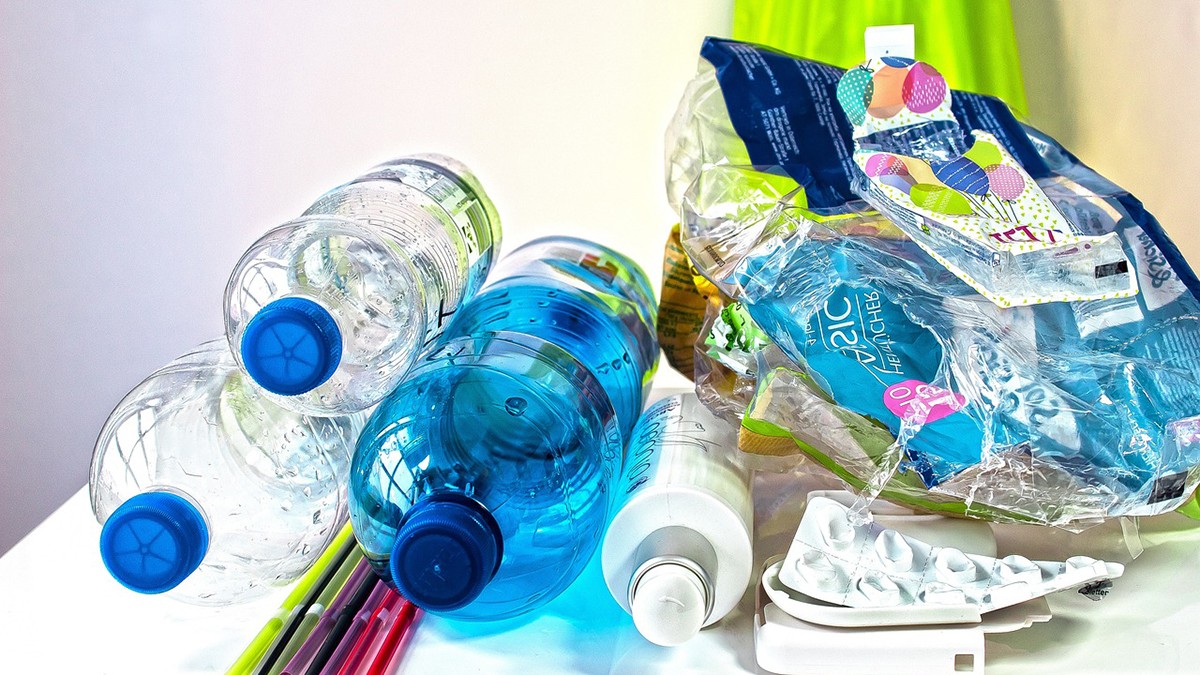